Charcoal Briquette Machine | Coal Press Machine
Model | WD-CB180 |
Capacity | 1000kg/h |
Power | 22kw |
Dimension | 2250*1400*600mm |
Weight | 1300kg |
+8617329326135 |
The charcoal briquette machine, also known as the coal press machine, utilizes the principle of screw extrusion to compress coal powder or other raw materials into briquettes. With a capacity of 500-1000kg/h, this machine is efficient for producing high-density charcoal rods.
These charcoal rods have a high calorific value, making them ideal for applications such as barbecue charcoal and home heating. Their economic benefits are significant due to their energy efficiency and the demand for charcoal in various industries.
In regions like Africa and Southeast Asia, where wood is abundant and charcoal plays a key role in food culture, the demand for charcoal remains high. This has made the charcoal briquette machine highly popular in these markets.
Raw materials of charcoal briquette machine
The charcoal extruder machine primarily uses materials such as carbon powder, coal powder, cow dung, grass powder, and cultured bacteria. Preparing these raw materials properly is crucial for optimal performance of the machine.
To prepare the materials, follow these steps:
- Carbon powder. Combine 100 grams of carbon powder with 30 to 40 grams of water and 5 to 10 grams of binder. This mixture ensures the right consistency for extrusion.
- Other raw materials. Similarly, adjust the amounts of water and binder according to the specific requirements of materials like coal powder, cow dung, or grass powder.
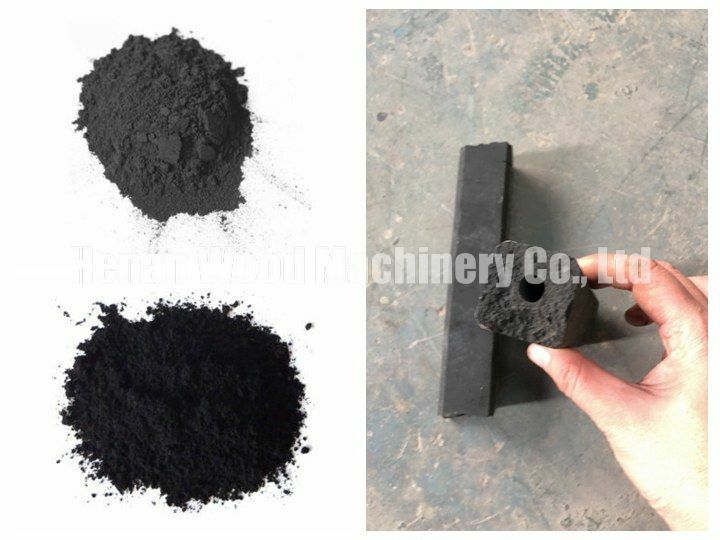
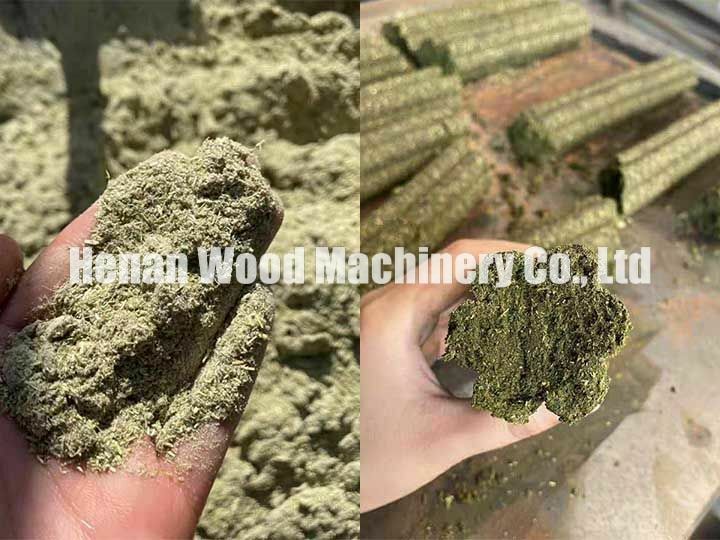
The precise preparation and mixing of these materials are essential for producing high-quality charcoal briquettes. The right balance of water and binder helps in achieving the desired density and durability of the briquettes.
Properly prepared materials ensure efficient operation of the charcoal extruder machine and result in a consistent, high-quality end product.
Charcoal extruder machine structure
The coal press machine mainly includes a feeding port, a reducer, propel spirals, an output shaft, and a motor. The shaft seat and the machine body are rigidly connected with high concentricity.
Each part has been debugged many times to help the whole machine run stably.
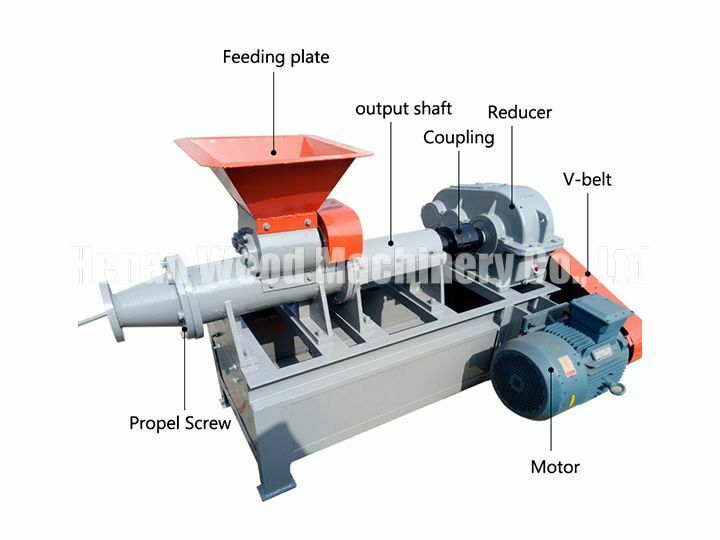
Component of charcoal extruder machine
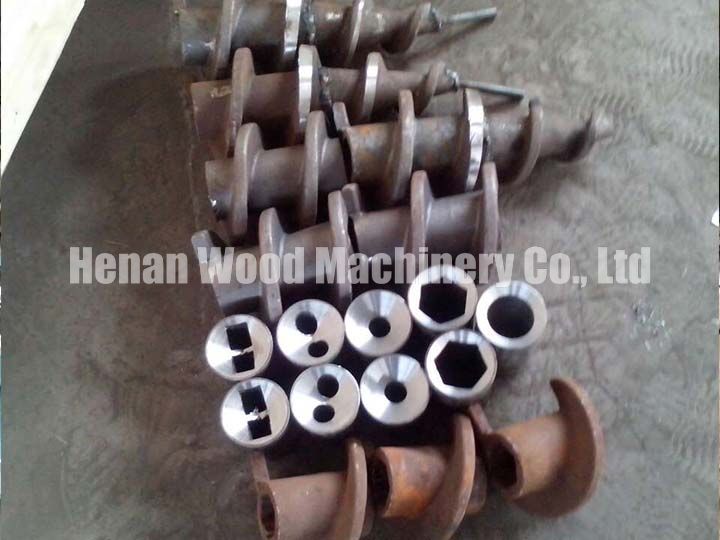
- The spiral of the charcoal briquette machine consists of three sections.
- The front section of the spiral can be adjusted to control whether the finished product is hollow or solid.
- To switch between different product types, the front section of the spiral is the only part that needs to be replaced.
- Charcoal briquette machines come with various shapes of model dies.
- These model dies allow for the extrusion of charcoal briquettes in different shapes.
- Customizable die shapes provide flexibility for producing a variety of briquette designs.
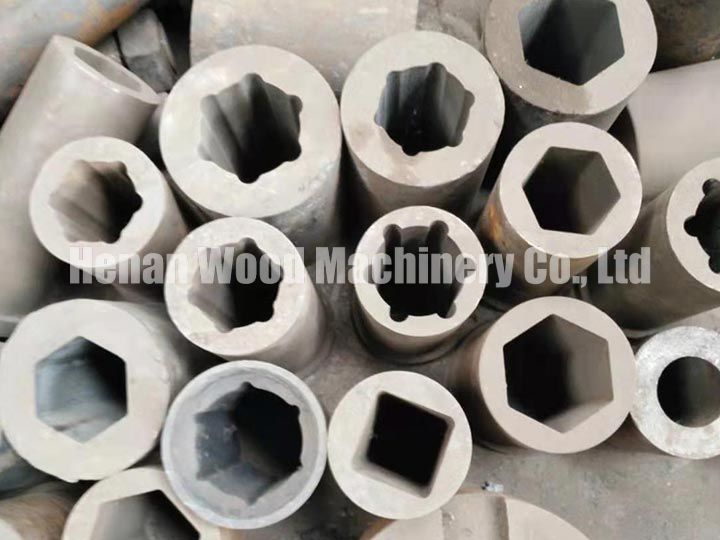
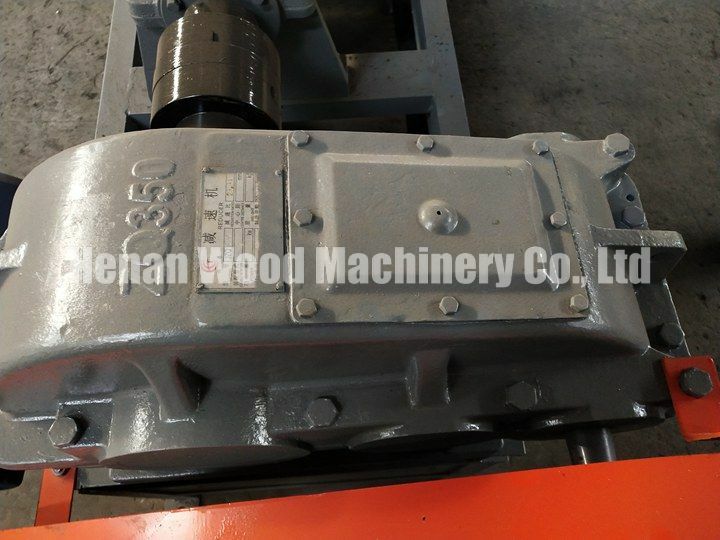
- Equipped with a hard tooth surface reducer for enhanced durability.
- Compact design ensures the charcoal briquette machine takes up less space.
- The machine features a strong bearing capacity, enabling efficient operation.
Working principle of coal press machine
The working principle of the coal press machine involves a series of mechanical processes that transform powdered coal into solid briquettes of various shapes. Here’s how it works:
- The electric motor transmits power to the machine through a belt pulley.
- This power drives the propulsion shaft, which begins to rotate.
- Attached to the propulsion shaft is a screw propeller, which pushes the coal material forward.
- The coal material is then compressed and forced through the forming die, where it takes on the desired shape.
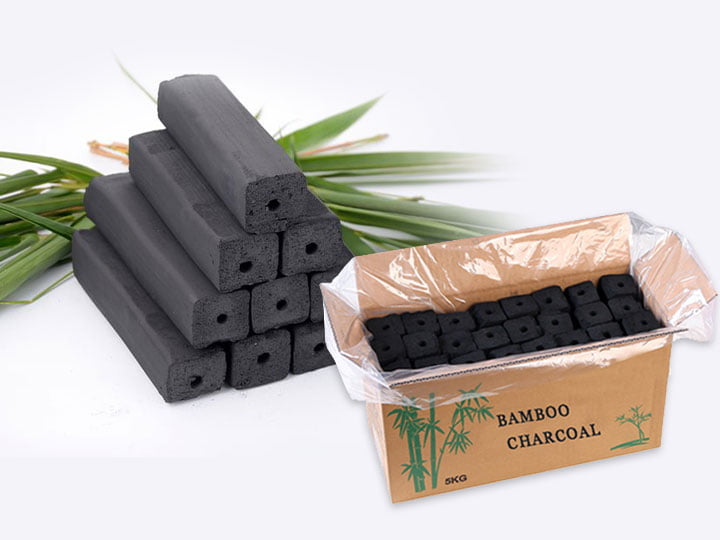
Through this high-pressure process, the machine produces coal sticks or briquettes that are compact and suitable for use in different applications.
Parameters of charcoal briquette machine
Model | Capacity | Power | Dimension | Weight |
WD-CB160 | 500kg/h | 11kw | 2050*900*1250mm | 900kg |
WD-CB180 | 1000kg/h | 22kw | 2250*1400*600mm | 1300kg |
Operation precautions of charcoal extruder machine
Proper maintenance is essential to ensure the long-term performance and durability of the charcoal briquette machine. Following a consistent maintenance routine and adhering to precautionary measures can significantly extend the machine’s service life. Here’s how to maintain and care for your machine:
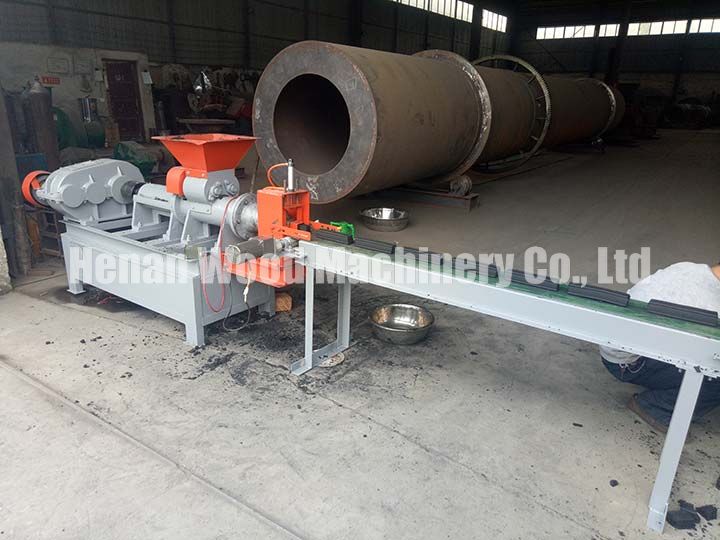
- Before starting, check all rotating parts for smooth operation and run the machine empty for 2–3 minutes to ensure no abnormal sounds.
- Ensure raw material particle size is ≤3mm; add water, binder, and curing agent in proper ratios, mix well, and let it sit for 24 hours before use.
- If the feed inlet is blocked, use wooden or bamboo sticks to clear it; avoid using metal tools to prevent machine damage.
- Regularly lubricate bearings with appropriate oil, and ensure bearing temperature does not exceed 60°C.
- When shutting down, stop unloading first, ensure all material is discharged, then turn off the machine; disassemble, clean, and reinstall the machine head for next use.
By following these steps, you can maintain optimal performance and extend the lifespan of your charcoal briquette machine.
Different cutting methods of charcoal briquette press machine
The video shows the three different charcoal cutting methods of briquette machines, they can cut the briquette into different shapes.
1. Automatic cutter
The automatic cutter features an advanced infrared sensor probe, which ensures precise and accurate cutting. This mechanism allows for easy control and customization of the cutting length based on specific requirements.
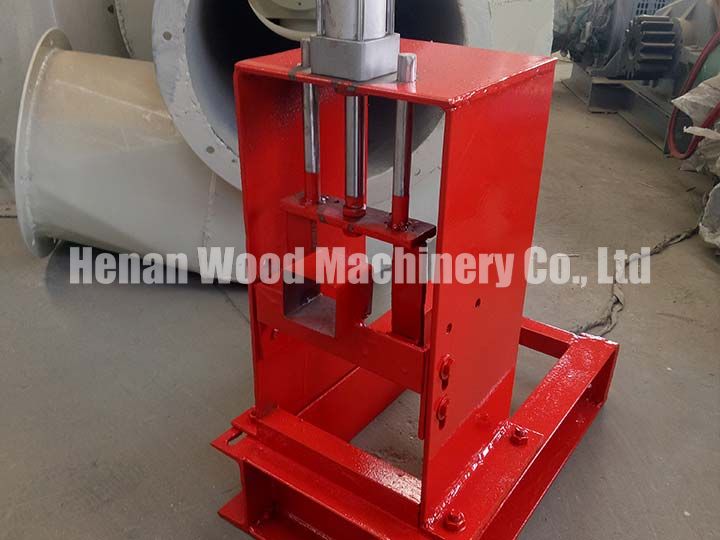
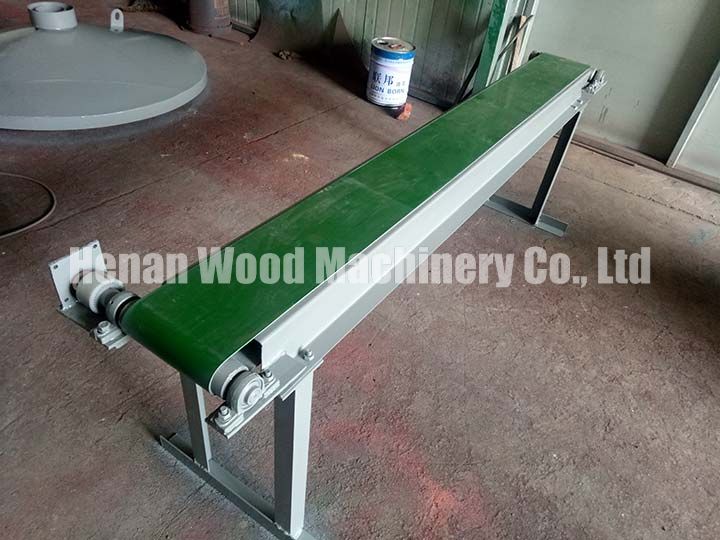
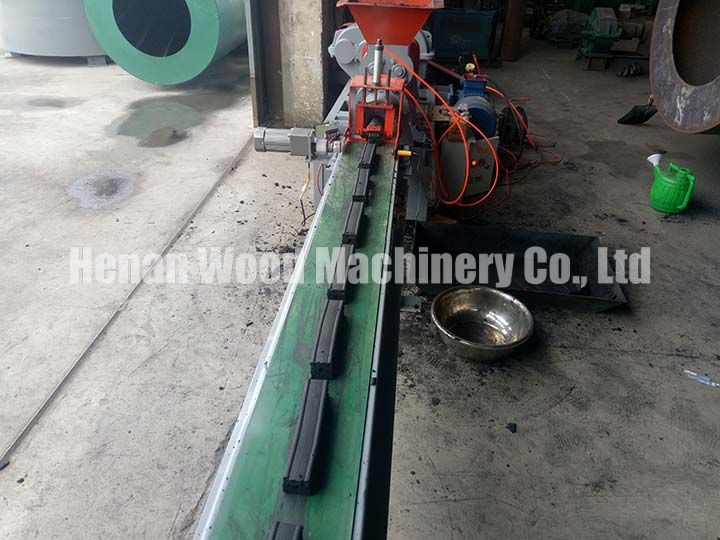
Key features include:
- Infrared sensor control. The cutting knife is guided by an infrared sensor, ensuring precision in every cut.
- Adjustable cutting length. The cutting length can be easily modified to suit various needs.
- Common cutting diameters. The standard cutting diameter is typically between 10-12cm, with a minimum diameter of 5cm for smaller applications.
This flexibility and precision make the automatic cutter an efficient solution for different cutting tasks.
2. CNC charcoal cutter machine
The cutter is equipped with a CNC numerical control system, offering a wide range of cutting lengths from 3 to 40 cm, with the shortest being 2.5 cm. This advanced system ensures flexibility and precision in meeting various cutting requirements.
Key features include:
- Wide cutting range. The CNC control allows cutting lengths between 2.5 cm to 40 cm, providing versatility for different needs.
- Environmentally resilient. The cutter operates efficiently without being affected by environmental factors such as strong light or dust, ensuring a stable cutting process.
- Compact design. Its small size makes it easy to transport, saving valuable space during shipping.
These features make the cutter a reliable and efficient tool for diverse cutting applications.
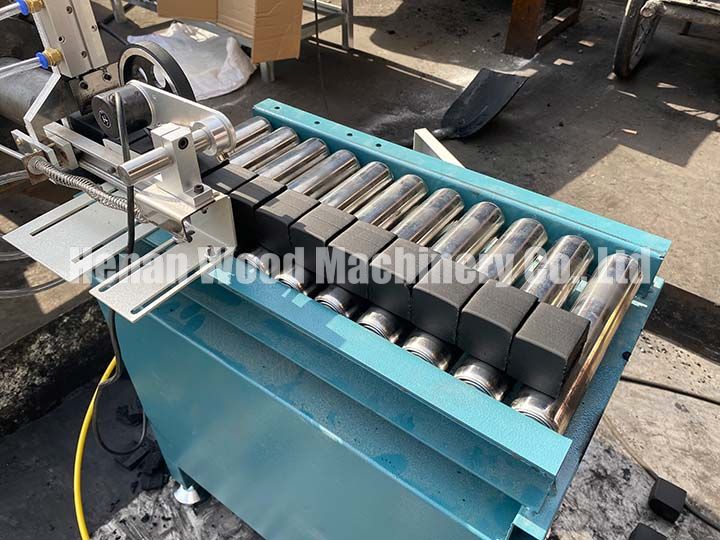
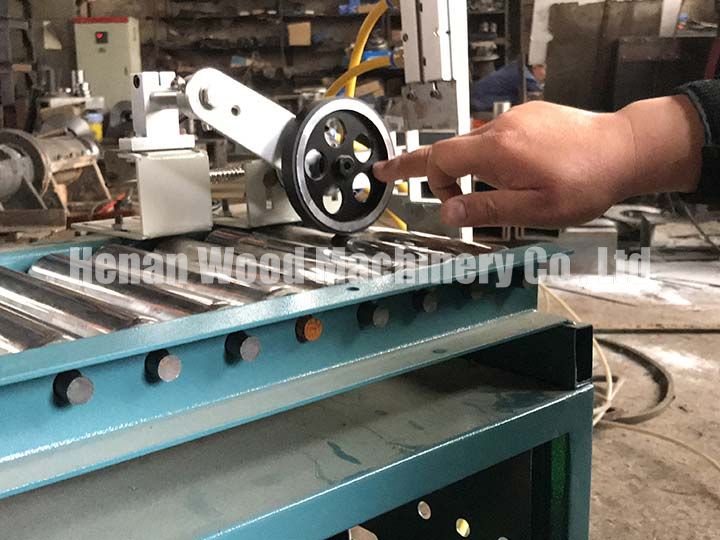
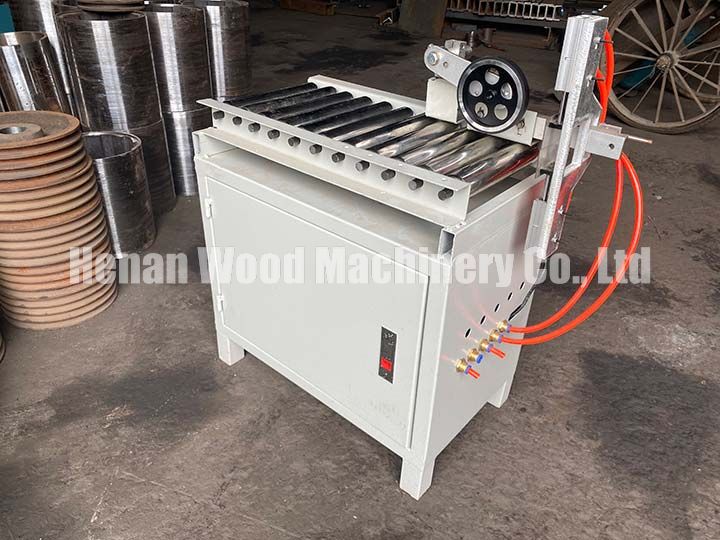
3. Cubic charcoal briquette cutting machine
The cutter produces square coal cubes with an edge length of 2.5 cm, providing uniform and precise cuts. Its design primarily includes a hob and a baffle to ensure consistent performance.
Key details:
- Cube dimensions. The cutter shapes coal into 2.5 cm edge-length cubes, offering uniformity in size.
- Core components. The system features a hob and baffle, essential for smooth and efficient cutting.
- Conveyor belt. The standard configuration includes a 1.5-meter conveyor belt, with options for customization based on specific needs.
This configuration ensures efficient coal cutting and transport for various production setups.
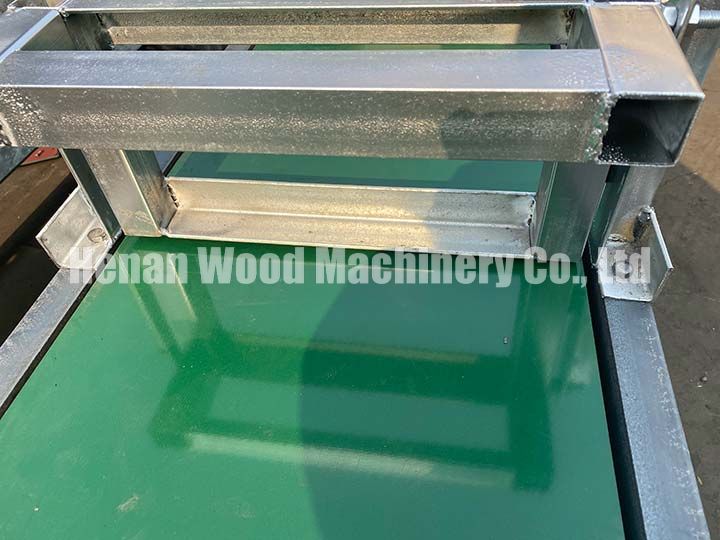
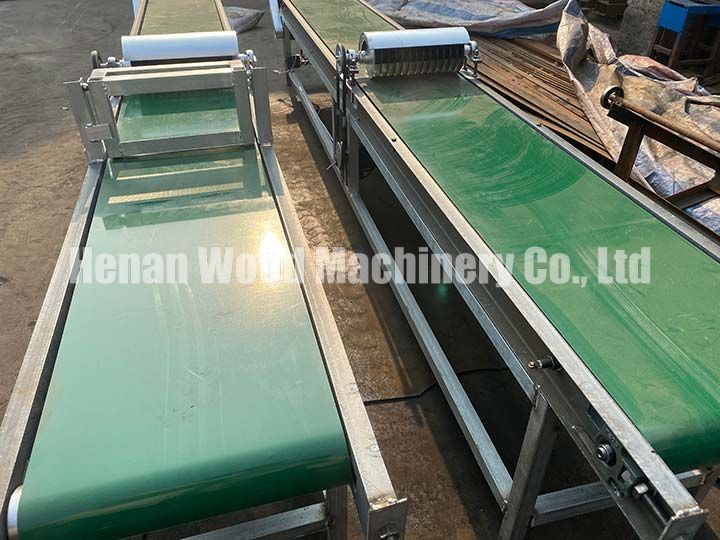
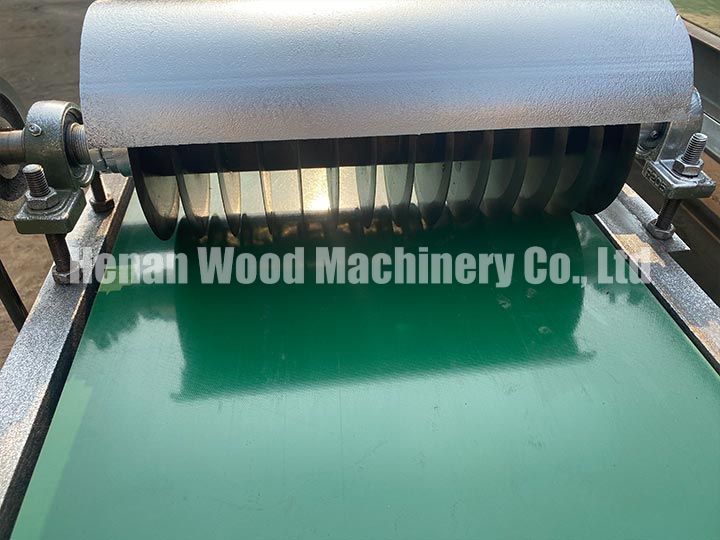
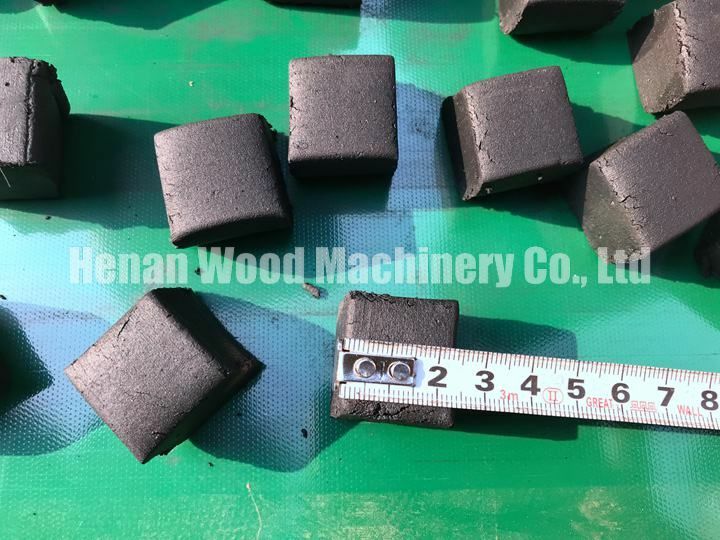
How to make high-quality coal briquettes?
To produce high-quality coal briquettes, several factors must be considered, as they directly influence both the price and durability of the final product.
As a coal press machine user, improving the quality of coal sticks is essential to maximizing efficiency and profitability. So, how can you enhance the quality of coal briquettes? Here are some key methods:
- Keep raw material sizes small—pulverized coal under 8 mm and charcoal powder under 1 mm—for smooth, compact briquetting.
- Hold moisture content at 10–15 % to maximize binding and prevent crumbling.
- Select a binder that matches the feedstock to enhance strength and density of the briquettes.
- Maintain consistent, proper press pressure so every coal stick comes out uniformly firm and solid.
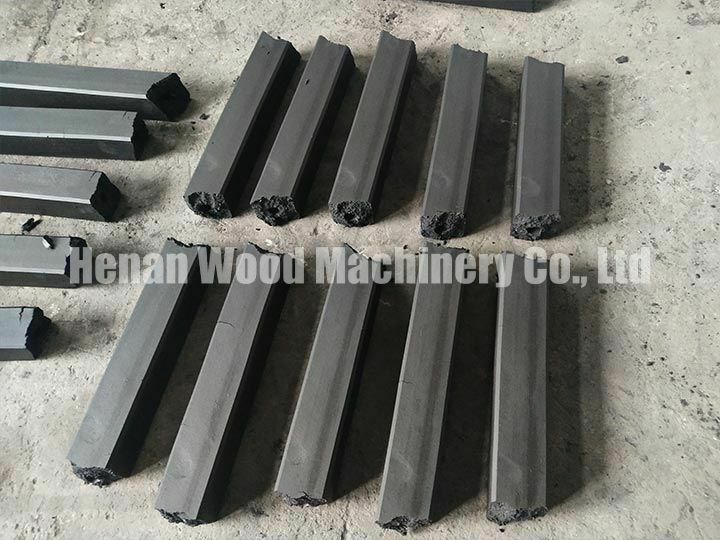
By following these methods, you can significantly improve the quality of your coal briquettes, ensuring better durability and market value.
Comparison of sawdust briquette machine and charcoal briquette machine
Because of the similar outlook and name, some customers are always confused about them. Shuliy machinery will introduce the differences between a sawdust briquette machine and a charcoal briquette making machine.
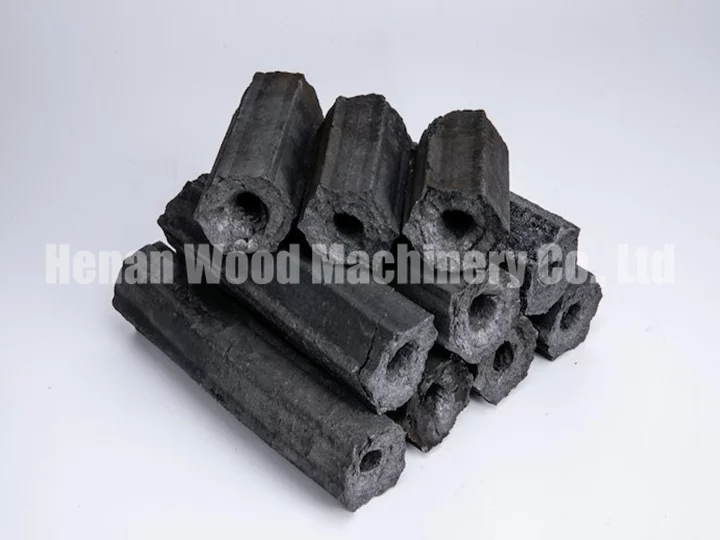
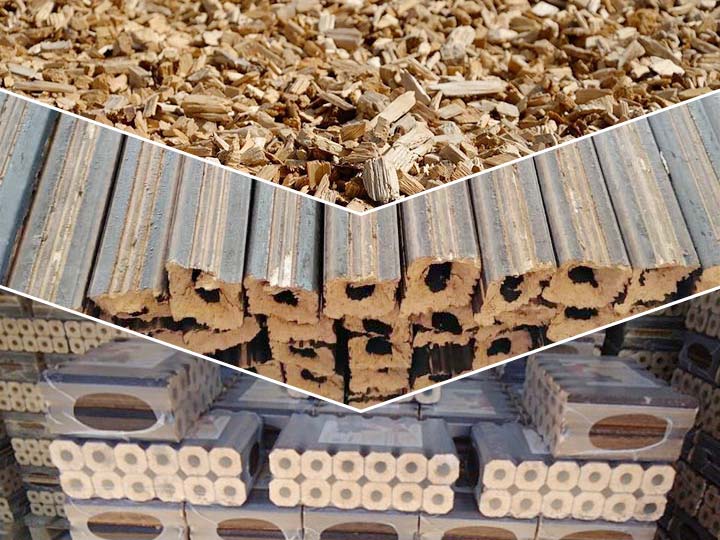
Raw materials
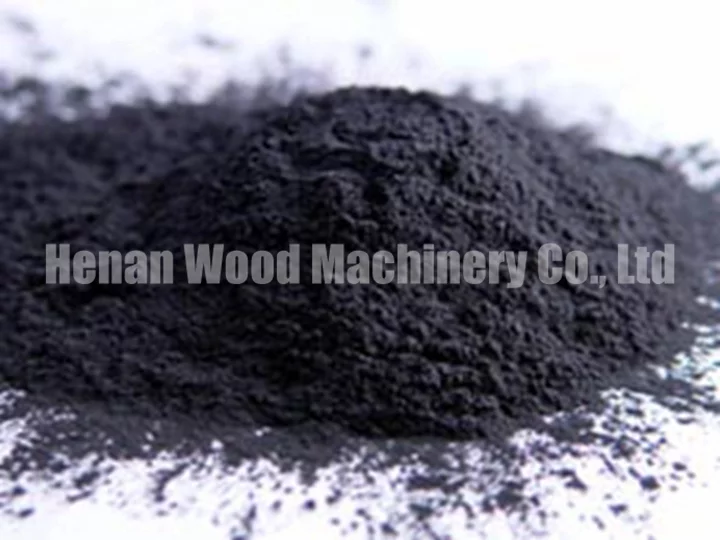
The sawdust briquette machine copes with small wooden or biomass chips, like sawdust, rice husk, and bamboo chips, which are 3mm to 5mm.
The raw material can also be logs or large branches, then they will be crushed by a drum wood chipper or wood hammer mill first.
However, the raw materials of charcoal briquette should be coal powder, which has been mixed with water and adhesive in advance.
Working principle
The sawdust briquette machine makes biomass stick by high temperature and pressure. At the end of the die head, there are three heating circle devices to heat the biomass stick.
The coal pressing machine has no heating device. The density of the pulverized coal is increased by spiral rotation and extrusion, and the pulverized coal is formed through a die.
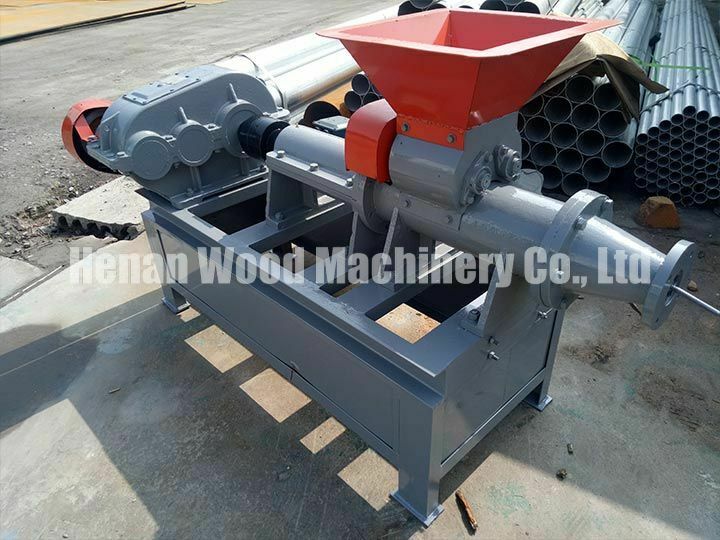
Final products
There are some pictures you can see below. It is pronounced that products made by sawdust briquette machines are yellow wooden sticks, meanwhile, products made by charcoal extruders are black coal sticks.
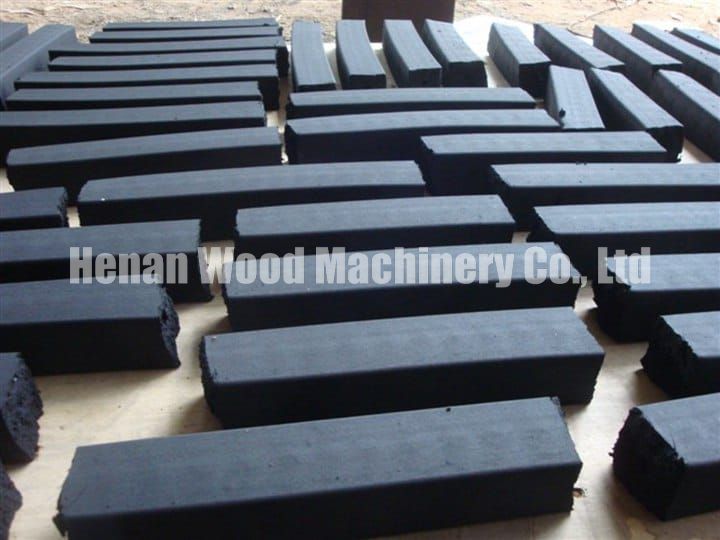
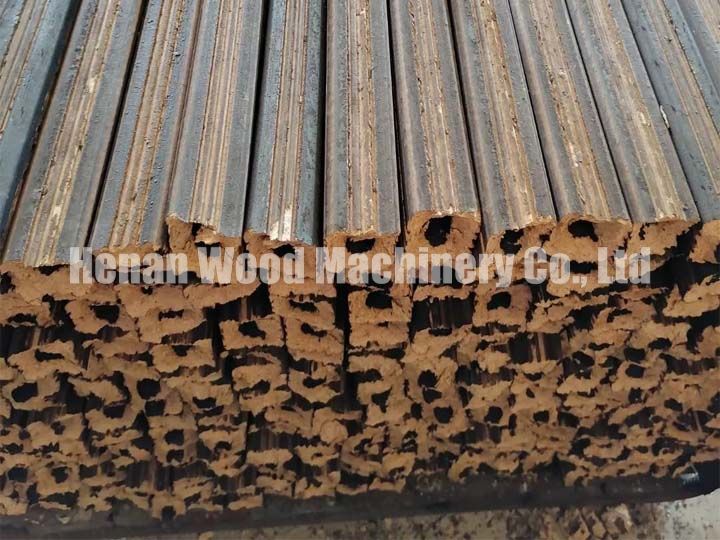
Why is the charcoal briquette machine so popular?
The popularity of charcoal briquette machines continues to grow, with sales maintaining a strong upward momentum. Industry experts have provided insights into why these machines are in such high demand. Here are the key reasons:
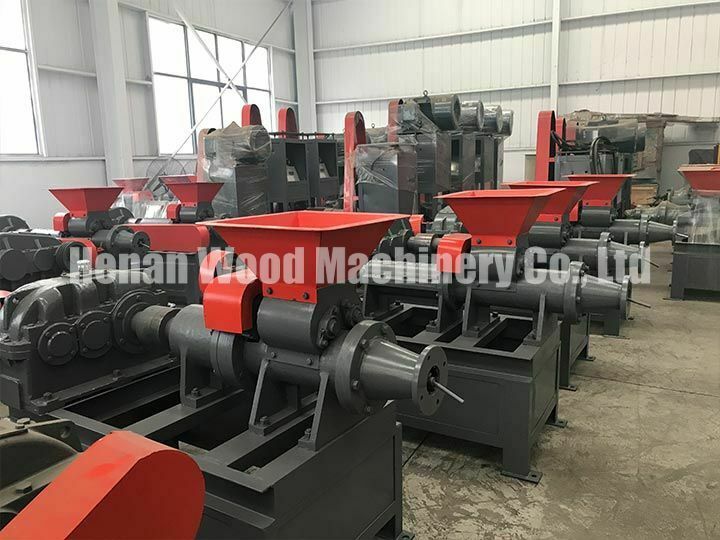
- Supports a wide range of raw materials like charcoal powder, coal powder, and grass powder for flexible production.
- Low machine cost with high return potential, making it a budget-friendly option for new or growing businesses.
- Produces high-density charcoal with low ash, no smoke, and a calorific value of 5500–7000 kcal/kg.
- Widely used for BBQ, heating, and industrial applications due to its superior quality.
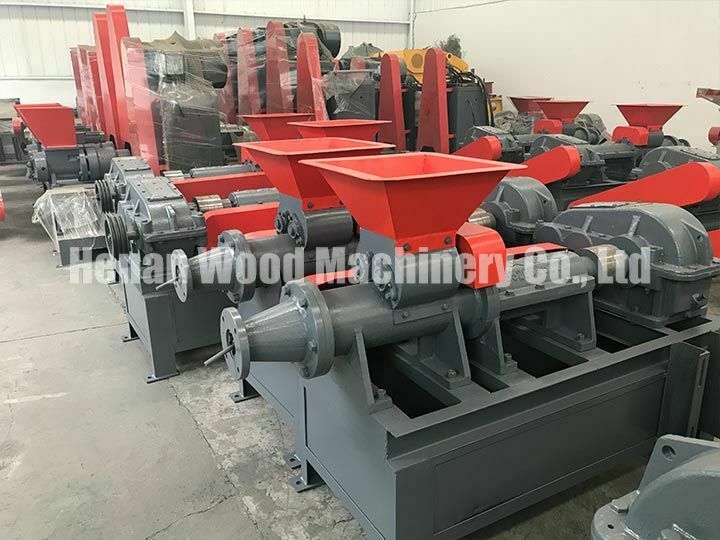
These factors collectively explain why the charcoal briquette machine is so popular in the market.
Our successful case of an Iraqi customer
Our company’s charcoal briquette extruders are very popular and have been exported all over the world. Recently, we had a successful case with a customer in Iraq.
Our customers in Iraq consulted us about charcoal briquette making machines, our sales manager Beco learned that he was just starting the coconut shell charcoal business and wanted to try it first to see how it works, so Beco recommended WD-CB180 to him for its moderate yield.
Finally purchased two of them and one charcoal pulverizer. Now those machines have been shipped to Iraq.
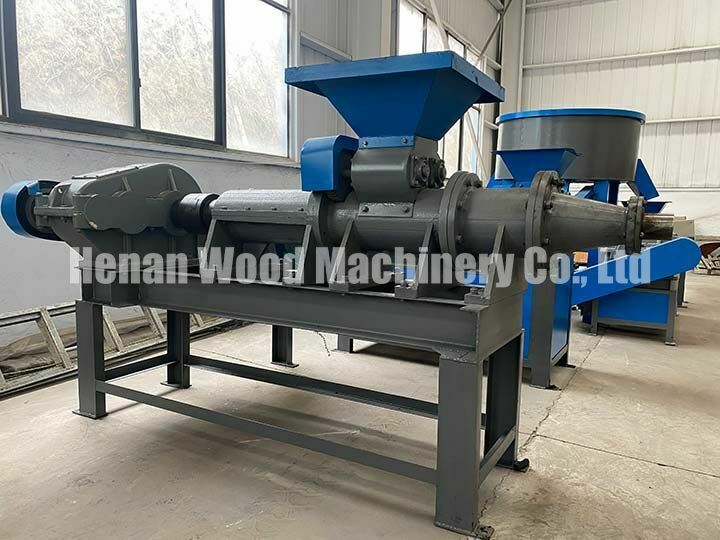
Leave your message!
If you’re looking for a reliable and efficient solution for producing high-quality charcoal briquettes, our Charcoal Briquette Machine is the ideal choice.
Our machines are designed with durability and performance in mind, ensuring long-term value and minimal maintenance. Additionally, our expert team is committed to providing excellent customer support and tailored solutions to meet your specific needs.
Don’t miss out on the opportunity to enhance your production capabilities and achieve superior results. Contact us today for a detailed quote and discover how our Charcoal Briquette Machine can benefit your business. Let us help you take your operations to the next level with our advanced and reliable machinery.
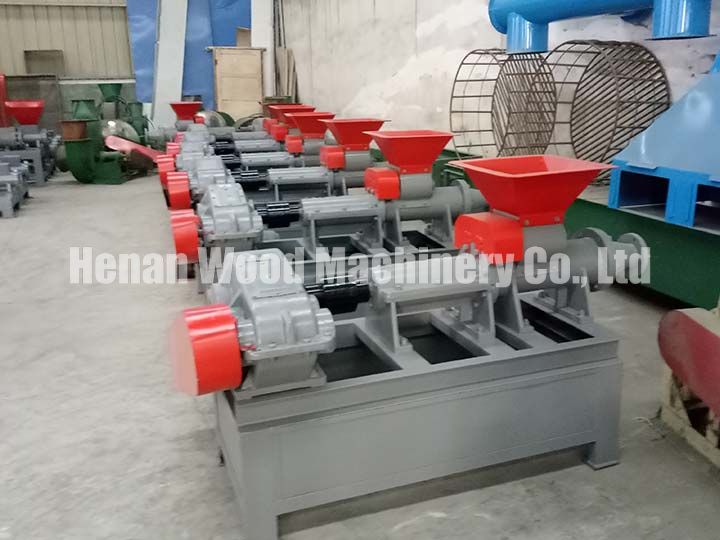
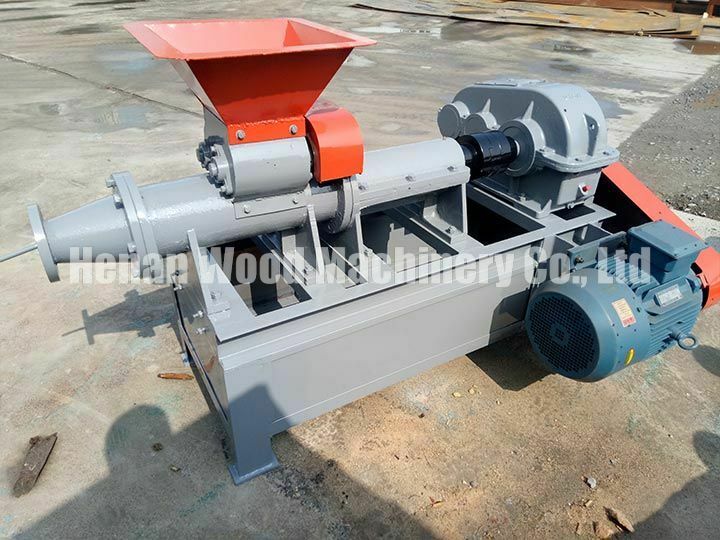
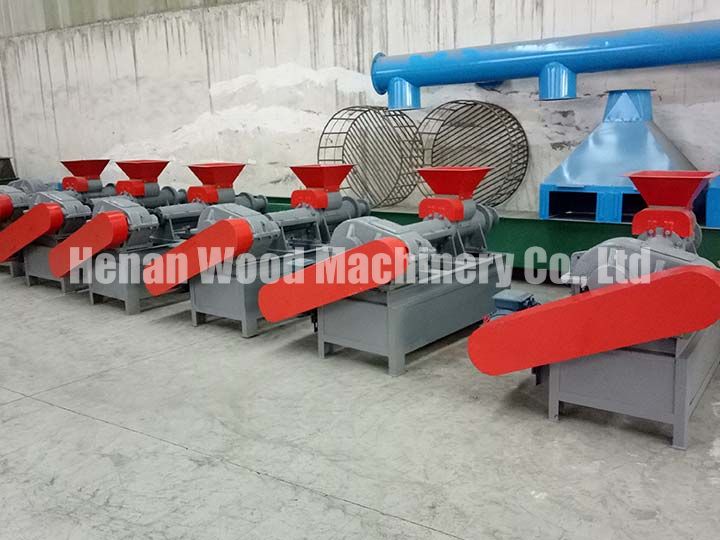