Kontinuierlicher Karbonisierungsofen
Modell | WD-CF1200 |
Durchmesser (mm) | 1200 |
Kapazität (kg/h) | 1200-1500 |
Hauptleistung (kW) | 20 |
Karbonisierungstemperatur (℃) | 500-800 |
Lüfterleistung (kW) | 5.5 |
Der Durchlaufkarbonisierungsofen ist ideal für die Verarbeitung verschiedener Biomassematerialien wie Holzspäne, Reisschalen und Palmenschalen. Mit einer Kapazität von 1200–1500 kg/h unterstützt diese Maschine eine kontinuierliche Beschickung und ermöglicht so eine unterbrechungsfreie und effiziente Karbonisierung.
Das System verfügt über eine geschichtete Karbonisierung, eine intelligente Steuerung und eine automatische Sammlung von Nebenprodukten wie Teer und brennbaren Gasen. Es geht effektiv auf die Herausforderungen traditioneller Karbonisierungsmethoden ein – Steigerung der Produktionseffizienz, Reduzierung der Arbeitsintensität und Förderung der nachhaltigen Nutzung erneuerbarer Ressourcen.
Rohstoffe des kontinuierlichen Karbonisierungsofens
Für den kontinuierlichen Karbonisierungsofen unterscheiden sich die Anforderungen an die Materialien von denen, die von den Hebe und horizontalen Karbonisierungsöfen verarbeitet werden. Dieser Ofen ist darauf ausgelegt, weichere und kleinere Materialien zu verarbeiten, die spezifische Kriterien für eine effiziente Karbonisierung erfüllen müssen.
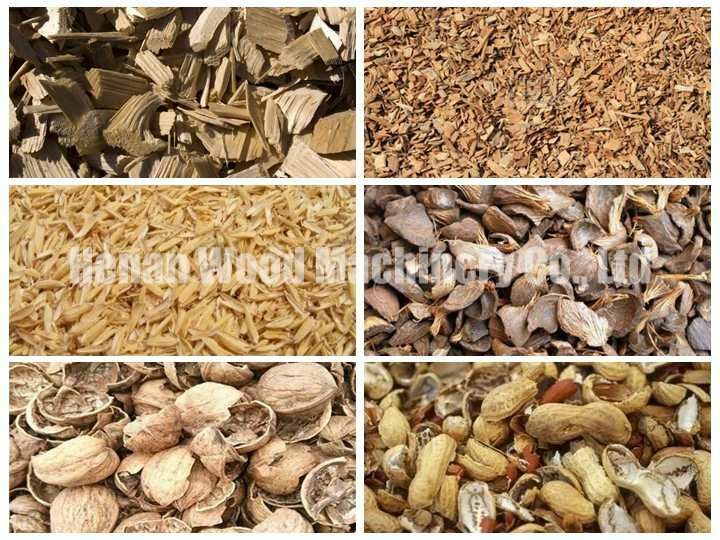
Materialgröße. Alle Materialien müssen klein und dünn sein, mit einer Größe von unter 10 Zentimetern.
Geeignete Materialien. Der kontinuierliche Karbonisierungsofen kann eine Vielzahl von kohlenstoffhaltigen Materialien verarbeiten, einschließlich:
- Erdnussschalen
- Pflanzenmaterial
- bellen
- Stroh
- Walnussschalen
- Kokosnussschalen
- Palmenschalen
- Sägespäne
Die Rohstoffe für den kontinuierlichen Karbonisierungsofen sollten idealerweise einen Feuchtigkeitsgehalt von unter 20 % haben. Wenn die Materialien diesen Grenzwert überschreiten, sollten sie mit einem biomass rotary dryer vorgetrocknet werden, um optimale Feuchtigkeitswerte zu erreichen.
Im Karbonisierungsofen finden Hochtemperatur-Trockendestillation und anaerobe Karbonisierungsprozesse statt, die eine hohe Karbonisierungsrate gewährleisten. Dieser Ofen ist eine ausgezeichnete Wahl für Holzkohleverarbeitungsanlagen und bietet eine effiziente, qualitativ hochwertige Holzkohleproduktion.
Struktur des kontinuierlichen Karbonisierungsofens
Der kontinuierliche Karbonisierungsofen besteht aus mehreren Schlüsselkomponenten: Spiral- und Flachzuführungssystemen, dem Hauptofenkörper, der Kondensationsaustragseinheit, dem Flammenkopf, dem Verbrennungsbecken, der Reinigungsausrüstung und dem Stromverteilerschrank.
Während des Betriebs durchläuft das Material nacheinander eine Vorwärmzone, eine Hochtemperatur-Karbonisierungszone und eine Kühlzone, um den Karbonisierungsprozess effizient abzuschließen.
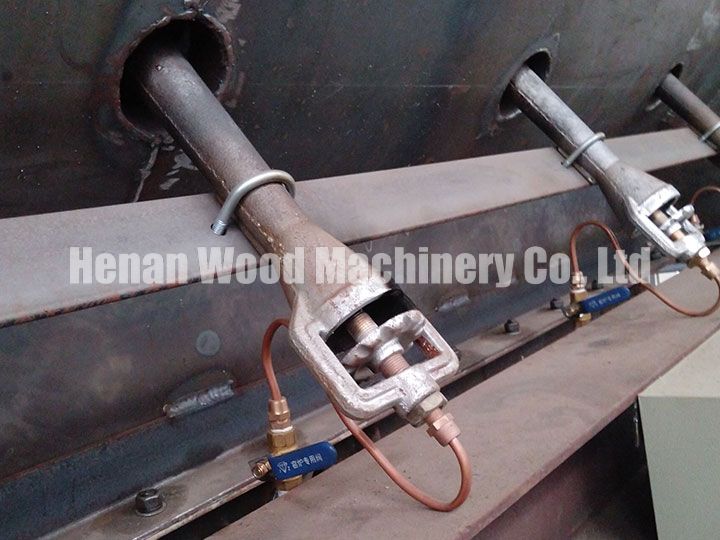
Zündkopf des Brennpools
- Das Modell WD-CF1200 verfügt über insgesamt 18 Zündgeräte.
- Das Modell WD-CF1200 verfügt über insgesamt 16 Zündgeräte.
- Diese Zündvorrichtungen werden verwendet, wenn Flüssiggas als Wärmequelle für die Maschine gewählt wird.
Brennpool der Sägemehlkohlemaschine
- Das Brennbecken in der Maschine zur Herstellung von Holzkohle aus Sägemehl ist ein kontrollierter Verbrennungsbereich.
- Es erzeugt die nötige Wärme, um den Karbonisierungsprozess effizient voranzutreiben.
- Dies trägt dazu bei, im gesamten Ofen konstante Hochtemperaturbedingungen aufrechtzuerhalten.
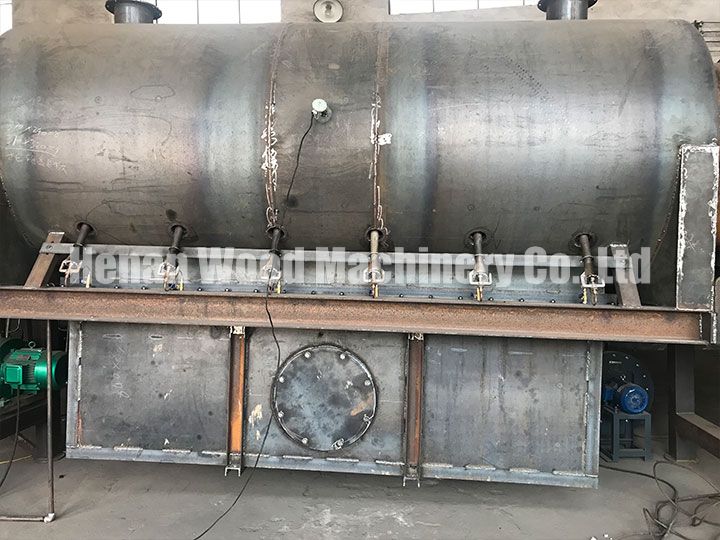
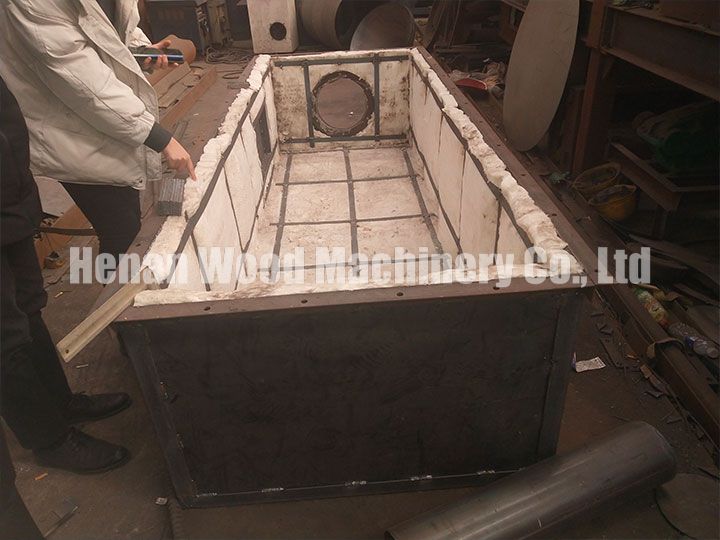
Innere Struktur des Brennpools
- Das Verbrennungsbecken besteht aus 4 mm dickem Q235-Stahl für eine lange Lebensdauer.
- Es ist mit einer 5 cm dicken Schicht Hochtemperatur-Steinwolle isoliert und sorgt so für eine hervorragende Wärmespeicherung.
- Steinwolle ist leichter als herkömmliche feuerfeste Steine und erleichtert so den Transport.
- Die Steinwolle bietet im Vergleich zu herkömmlichen Materialien eine bessere Wärmedämmung.
Innere Mineralwolle des Karbonisierungsofens
- Hergestellt aus 310er-Edelstahlplatten und Steinwolle für längere Haltbarkeit.
- Bietet eine verbesserte Abdichtung und reduziert den Wärmeverlust.
- Gewährleistet eine effiziente Wärmespeicherung in der Karbonisierungskammer.
- Hält optimale Temperaturen im Karbonisierungsbereich aufrecht und sorgt so für konsistente Ergebnisse.
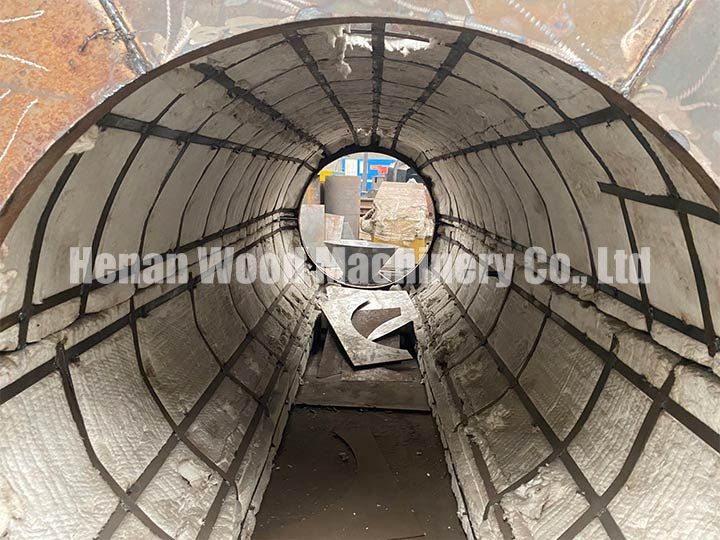
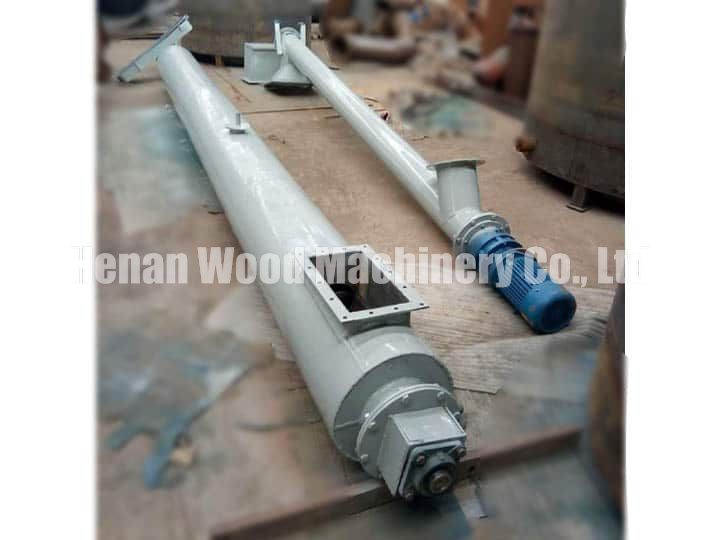
Schneckenförderer und Kühlabgabegerät
- Das Kühlauslassgerät kann entweder an eine Wasserpumpe oder eine Wasserleitung angeschlossen werden.
- Es kühlt die Hochtemperaturkohle, um eine Selbstentzündung beim Materialaustrag zu verhindern.
Innere Struktur des Schneckenförderers
- Die innere Struktur des Schneckenförderers besteht aus einem rotierenden Schneckenblatt.
- Das Schraubenblatt ist in einem zylindrischen Rohr untergebracht.
- Dieses Design transportiert Materialien effizient durch mechanische Bewegung.
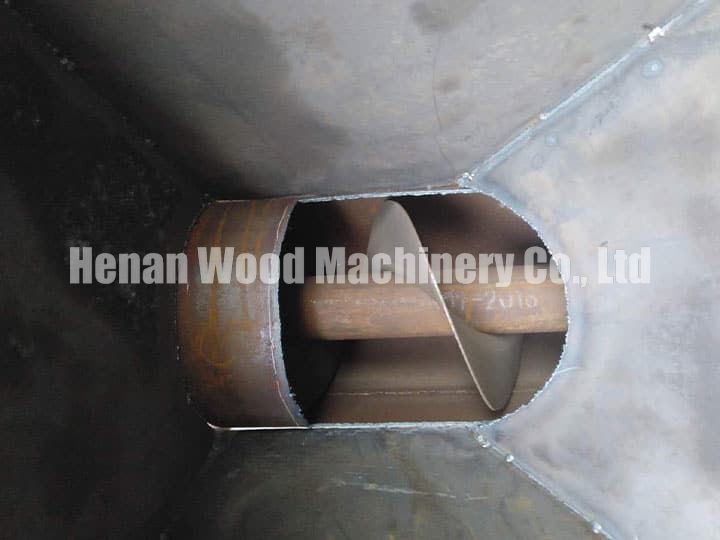
Wie man Reishülsen in einem kontinuierlichen Karbonisierungsofen karbonisiert?
Um Reisschalen in einem kontinuierlichen Karbonisierungsofen zu karbonisieren, gehen Sie folgendermaßen vor:
Vorheizung und Zündung
- Verwenden Sie Flüssiggas (LPG), um die Maschine zu zünden.
- Heizen Sie den Ofen etwa 1 Stunde lang vor. Für die Zündung werden etwa 20-30 kg Flüssiggas benötigt, das nur einmal gezündet werden muss.
- Das Vorheizen ist abgeschlossen, wenn die Temperatur zwischen 280 und 330 °C liegt.
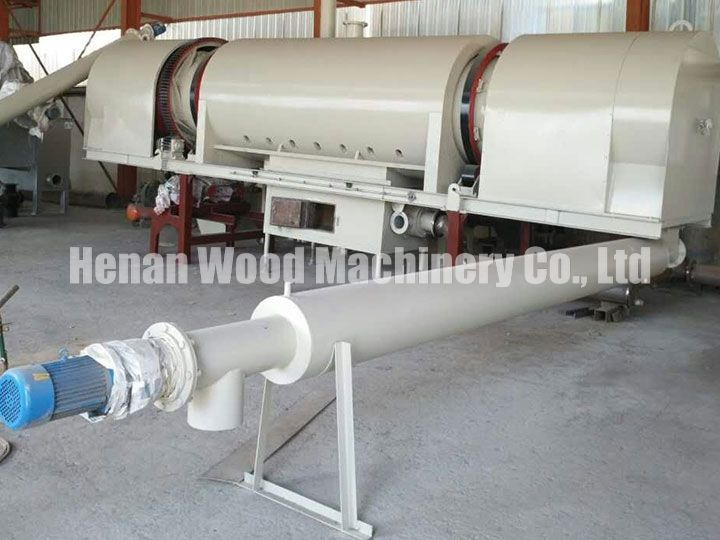
Karbonisierungsprozess
- Sobald die Vorheiztemperatur erreicht ist, beginnen Sie mit der Zugabe von Rohstoffen wie Reishülsen in den Ofen.
- Bei Reisschalen kann das Material ausgetragen werden, sobald der Ofen eine Temperatur von 280 °C erreicht hat.
- Zünden Sie die Brennkammer an und beobachten Sie nach 10-20 Minuten der Verkokung, ob im Brennbecken heißes Gas entsteht.
- Wenn brennbares Gas entsteht, zünden Sie das Gas an, damit es in der Brennkammer verbrennt.
- Sobald der Verbrennungsprozess beginnt, schalten Sie den Flüssiggasbrenner aus.
Zyklus und Kühlung
- Eine Karbonisierungsrunde dauert etwa 20 Minuten. Danach kann das Material entfernt und für einen neuen Zyklus durch frisches Rohmaterial ersetzt werden.
- Beim Austragen des Materials ist eine Kühlung erforderlich. Der Ofen verfügt über einen Doppelschichtkondensator, der mit zirkulierendem Wasser gefüllt ist, um das karbonisierte Rohmaterial vor dem Austrag abzukühlen.
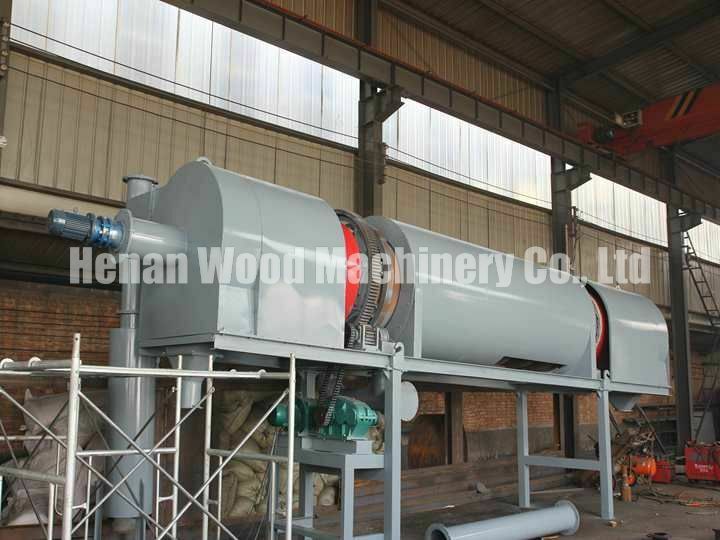
Parameter des kontinuierlichen Karbonisierungsofens
Modell | WD-CF800 | WD-CF1000 | WD-CF1200 |
Durchmesser (mm) | 800 | 1000 | 1200 |
Kapazität (kg/h) | 400-600 | 800-1000 | 1200-1500 |
Hauptleistung (kW) | 18.5 | 18.5 | 20 |
Karbonisierungstemperatur (℃) | 500-800 | 500-800 | 500-800 |
Lüfterleistung (kW) | 5.5 | 5.5 | 5.5 |
Der Durchlaufverkokungsofen wird nach dem Durchmesser des Ofens benannt, wobei größere Durchmesser die Verarbeitung von mehr Rohstoffen ermöglichen.
Unter den verschiedenen verfügbaren Modellen sticht das Modell WD-CF1000 aufgrund seiner ausgewogenen Leistung und seines Preises hervor, was es zu einer beliebten Wahl bei Kunden macht.
Seine moderate Größe bietet eine optimale Lösung für diejenigen, die eine effiziente Karbonisierung ohne die höheren Kosten suchen, die mit größeren Modellen verbunden sind.
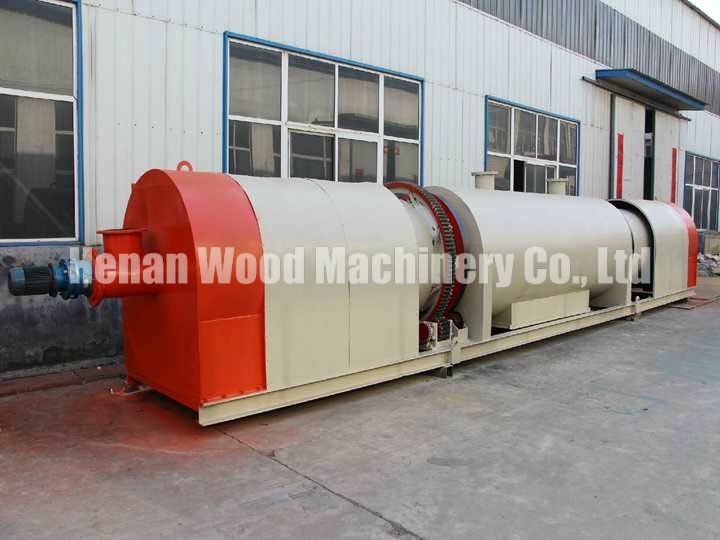
Eigenschaften des kontinuierlichen Karbonisierungsofens
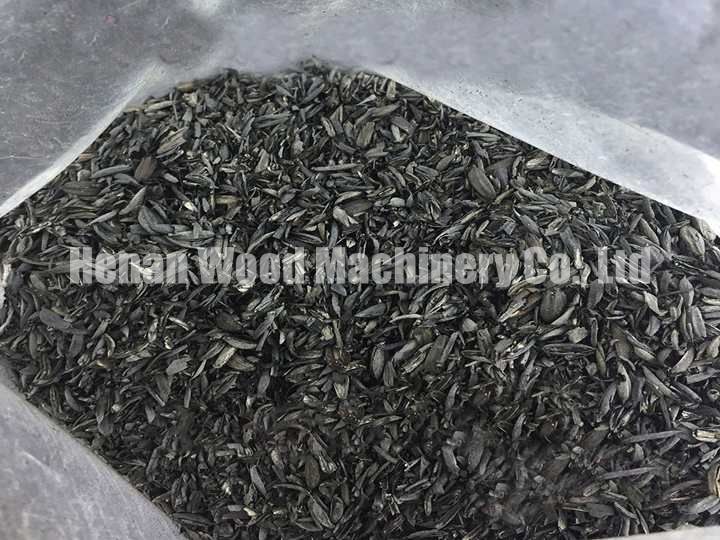
- Kontinuierliche Zuführung
- Der Ofen ermöglicht eine kontinuierliche Zuführung, Karbonisierung und Entladung, was die Effizienz im Vergleich zu traditionellen Batch-Anlagen erheblich verbessert.
- Hohe Automatisierung
- Mit einem intelligenten Kontrollsystem reduziert es den Arbeitsaufwand und ersetzt manuelle Arbeit durch einen effizienteren automatisierten Prozess.
- Umweltfreundliches Design
- Verwendet sauberen Brennstoff und fortschrittliche Rauchentfernung, um Verschmutzung zu verhindern und eine kohlenstoffarme, nachhaltige Produktion zu unterstützen.
- Automatische Sammlung von Nebenprodukten
- Sammelt effizient Teer, Holzessig und Gas während der Karbonisierung zur umfassenden Nutzung erneuerbarer Energien.
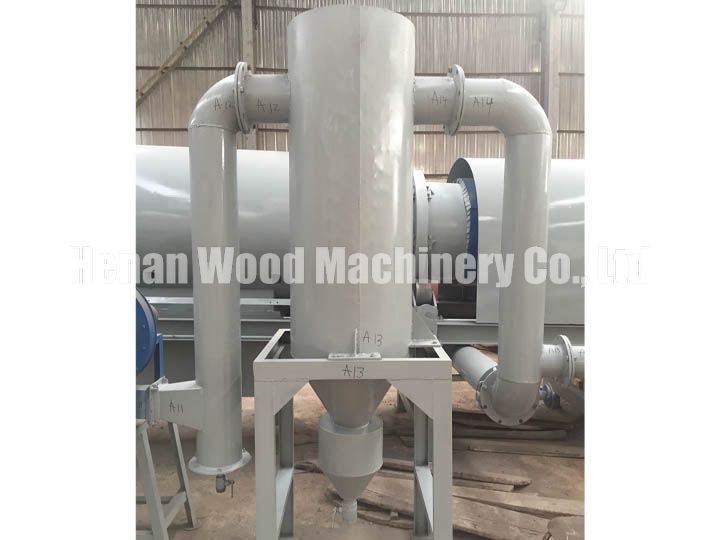
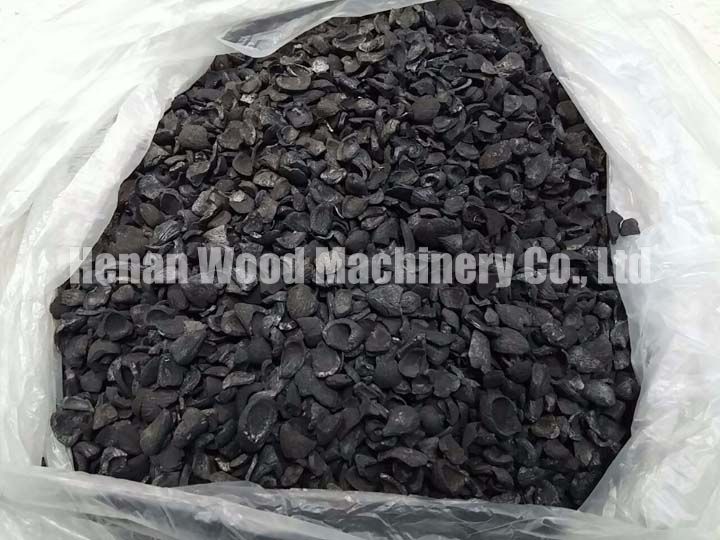
- Hochwertige Ausgabe
- Die Holzkohle ist ungiftig, geruchlos, mit einem Feuchtigkeitsgehalt von unter 5% und brennt länger – ideal als sauberer, effizienter Brennstoff.
FAQs zum kontinuierlichen Karbonisierungsofen
Was ist die Heizquelle der Sägemehlkohlemaschine?
Der kontinuierliche Karbonisierungsofen verwendet Flüssiggas (LPG) als primäre Heizquelle, die typischerweise nur 15–20 kg pro Zyklus verbraucht. Nach 1 bis 1,5 Stunden Betrieb beginnt er, brennbares Gas zu produzieren, das dann zur Aufrechterhaltung des laufenden Betriebs verwendet werden kann – wodurch die Notwendigkeit für zusätzliches LPG entfällt. Dies macht LPG zu einer empfohlenen Wahl, um sowohl energieeffizient als auch kostenersparend zu sein.
Kann der Karbonisierungsofen nur Biomasse-Rohstoffe karbonisieren?
Neben Biomasse kann der kontinuierliche Karbonisierungsofen auch verschiedene Materialien wie Alufolie, Blechdosen, Haushaltsabfälle, Kunststoffe und elektronischen Abfall verarbeiten. Für die beste Leistung sollte die Materialgröße unter 10 Zentimetern gehalten werden, um eine effiziente Karbonisierung zu gewährleisten.
Was sind die Vorteile unseres kontinuierlichen Karbonisierungsofens im Vergleich zu anderen Herstellern?
Unser Ofen verfügt über eine größere Verbrennungskammer, Edelstahlkonstruktion und automatische elektrische Zündung. Er verwendet einen wasserkühlten Edelstahlventilator und ein teerfreies Direktverbrennungssystem, um eine höhere Effizienz und saubereren Betrieb zu gewährleisten.
Wie viel Platz benötige ich, um einen kontinuierlichen Karbonisierungsofen zu betreiben?
Jede Einheit benötigt einen Platz von 250–300 Quadratmetern, mit einer Mindestbreite von 10 Metern und einer Länge von 22 Metern. Der Betrieb einer Maschine erfordert ein Team von drei Arbeitern.
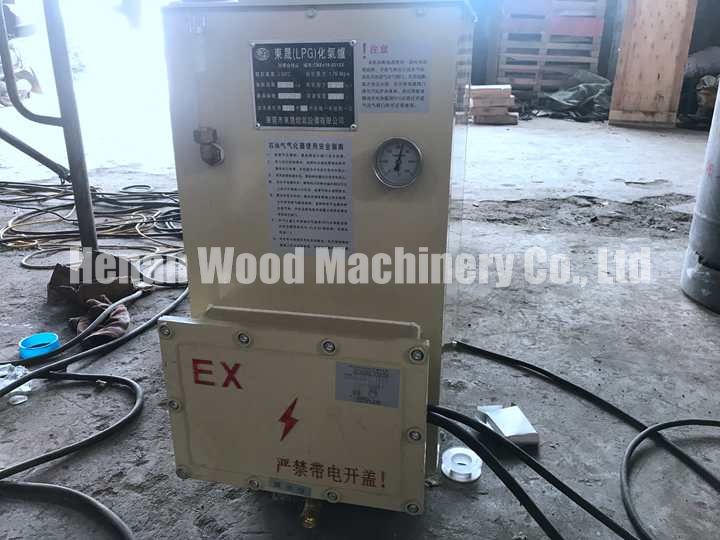
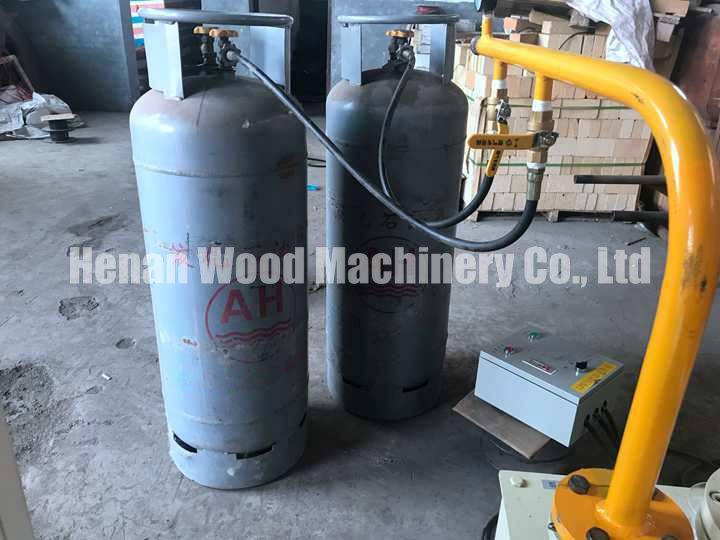
Wie produziert man Holzkohlebriketts?
Der verglühte Holzkohle kann zu Holzkohlepulver gemahlen werden und anschließend mit einem bestimmten Bindemittelanteil gemischt werden. Die Maschine Shuliy bietet verschiedene Ausrüstungen, um Holzkohle in verschiedenen Formen herzustellen.
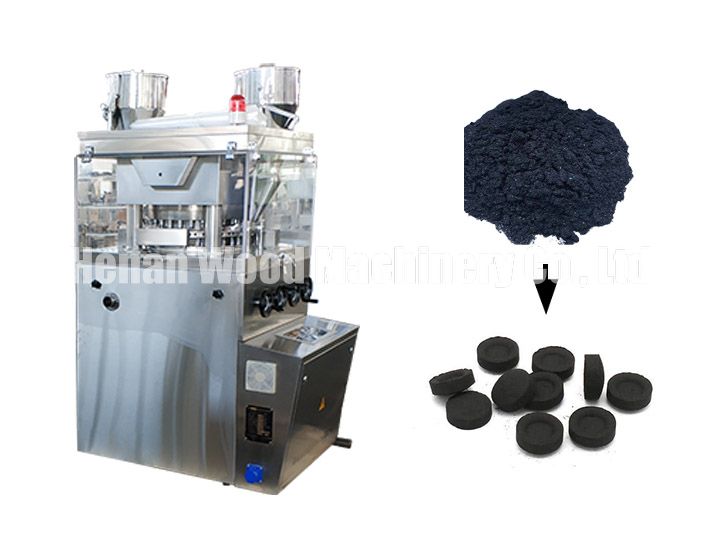
Verwendung der Shisha-Holzkohlemachine, um quadratische und runde Shisha-Holzkohle herzustellen. Die Größe, das Muster und die Form der Shisha-Kohle können alle angepasst werden.
Diese Waben-Kohlebrikettmaschine kann Holzkohle-Pulver zu Waben- oder Holzkohle-Ziegeln extrudieren.
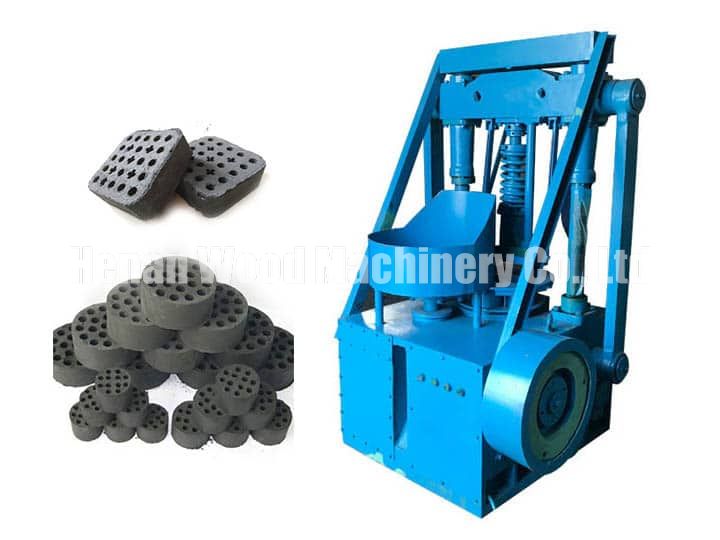
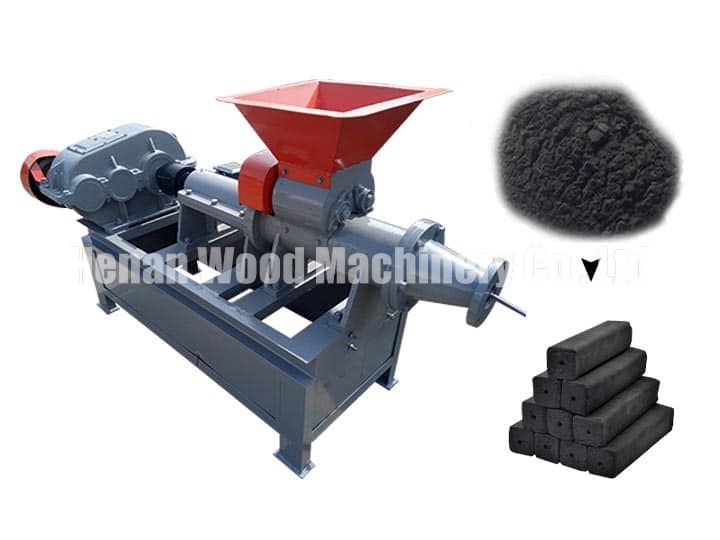
Die Holzkohle-Extrusionsmaschine verarbeitet das Holzkohle-Pulver zu regulären langen Stäbchen, die als Heizmaterial verwendet werden können.
Die BBQ-Holzkohlebrikettmaschine kann verwendet werden, um Holzkohle-Pulver zu kugelförmigen, quadratischen oder kissenförmigen Holzkohlebriketts zu extrudieren.
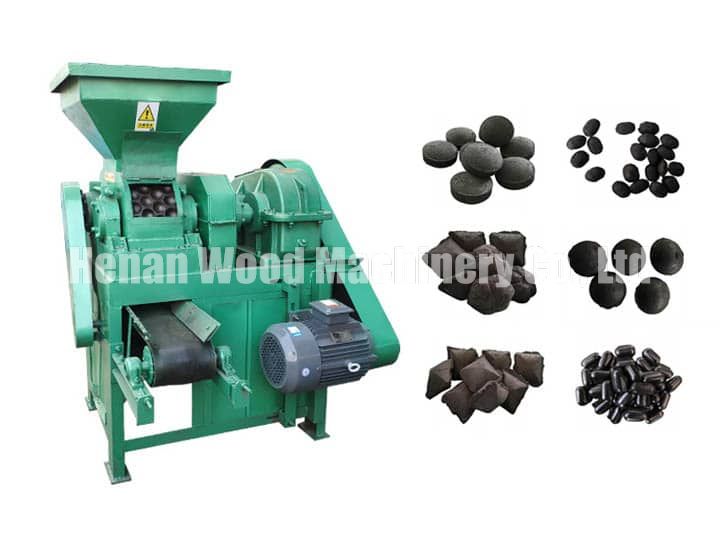
Laden und Lieferung der Sägemehlkohlemaschine
Ein Kunde in Ghana bestellte bei unserer Kohlenstoffmaschinenfabrik einen kontinuierlichen Karbonisierungsofen WD-CF1000 mit einer Produktionskapazität von 800–1000 kg/h.
Angesichts der wachsenden Nachfrage nach Grillkohle auf dem lokalen Markt wollte der Kunde in professionelle Karbonisierungsgeräte investieren, um den Start seines Holzkohleproduktions- und Vertriebsgeschäfts zu unterstützen.
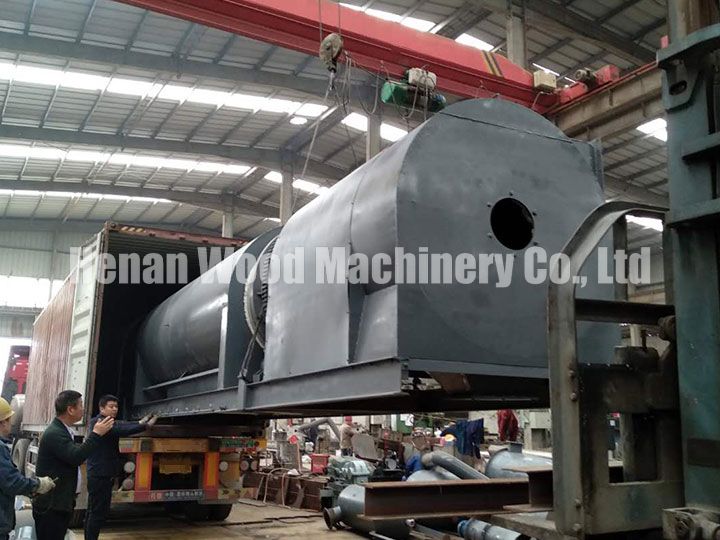
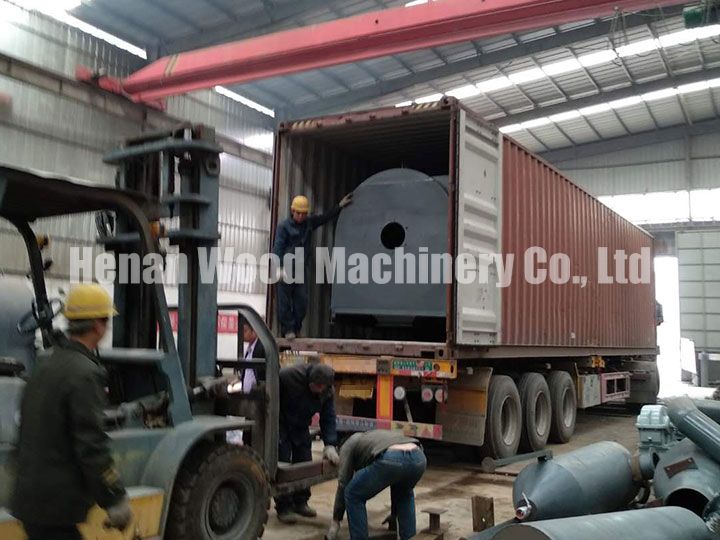
Fazit
Zusammenfassend lässt sich sagen, dass der kontinuierliche Karbonisierungsofen eine fortschrittliche und effiziente Lösung für die Karbonisierung einer breiten Palette von Biomassematerialien bietet. Durch die kontinuierliche Zuführung, die intelligente Steuerung und die automatische Sammlung von Nebenprodukten steigert es die Produktionseffizienz deutlich und minimiert gleichzeitig die Umweltbelastung.
Ob für die Holzkohleproduktion, Energieerzeugung oder nachhaltige Ressourcennutzung, diese Maschine stellt eine zuverlässige und kostengünstige Investition für Unternehmen dar, die ihre Karbonisierungsprozesse optimieren und zu einer saubereren, grüneren Zukunft beitragen möchten.
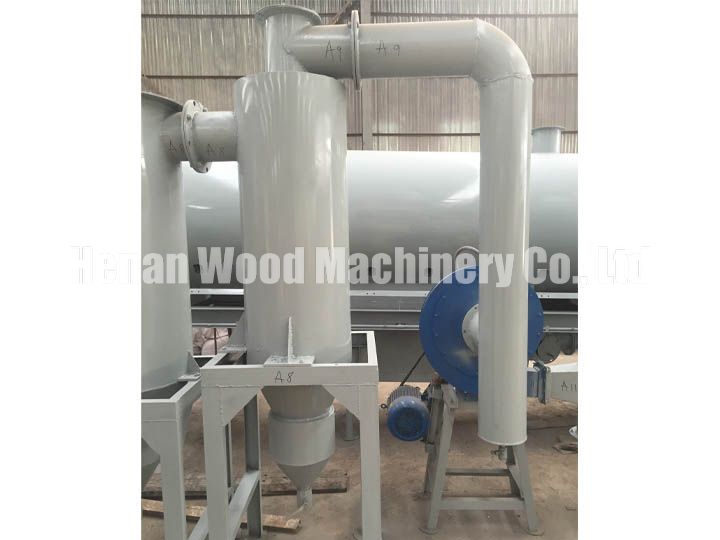