Sägemehlbrikettiermaschine | Biomasse-Brikettmaschine zu verkaufen
Modell | WD-WB50 |
Kapazität | 250-350 kg pro Stunde |
Leistung | 18,5 kW/22 kW |
Abmessungen | 1,7 * 0,7 * 1,4 m |
Gewicht | 700kg |
Die Sägemehlbrikettmaschine kann Abfallholzmaterialien wie Sägemehl, Reishülsen und andere Biomasse in hochdichte Brennstoffbriketts umwandeln. Mit einer Kapazität von 250–350 kg/h, diese Maschine komprimiert rohe Biomasse unter hohen Temperaturen und Druck und bildet feste Brennstäbe, die sowohl umweltfreundlich als auch effiziente Alternativen zu traditionellen Brennstoffen wie Holz und Kohle sind.
Die resultierenden Briketts haben eine kompakte Form, eine hervorragende Brennbarkeit und können auch in Schwelöfen weiterverarbeitet werden, was sie zu einer nachhaltigen Wahl für die Energieerzeugung macht. Diese Ausrüstung legt den Schwerpunkt auf die Abfallverwertung und steht im Einklang mit ökologischen Zielen, indem sie ansonsten entsorgte Materialien wiederverwendet.
Sägemehlbrikettiermaschine zu verkaufen
Die zum Verkauf stehende Biomasse-Brikettiermaschine ist vielseitig und in der Lage, ein breites Spektrum an Rohstoffen zu verarbeiten, darunter verschiedene Holzabfälle und Ernterückstände.
Es wandelt Materialien wie Sägemehl, Maisstängel, Sojabohnenstängel und Reisschalen in Sägemehlbriketts um und fördert so eine nachhaltige Kraftstoffproduktion.
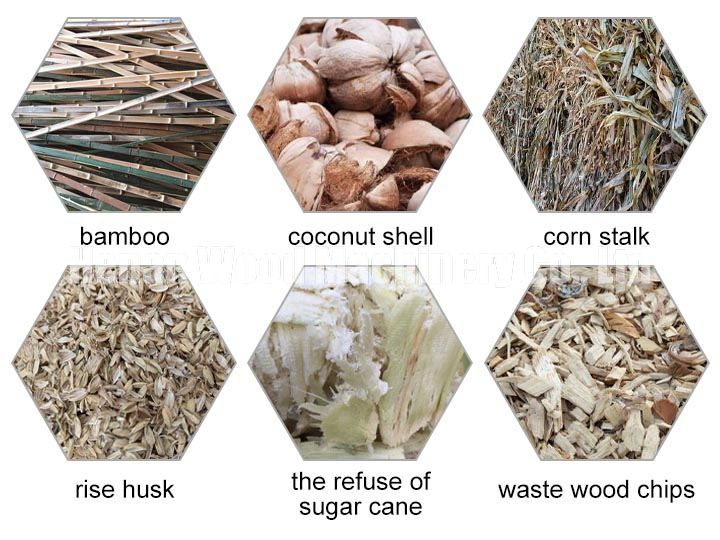
Bevor diese Materialien jedoch verarbeitet werden können, sind zwei wesentliche Schritte erforderlich:
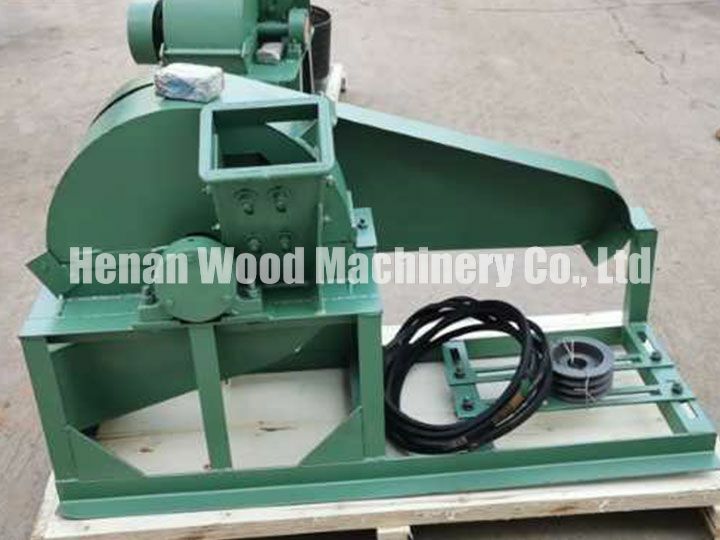
Zerquetschen
Die Rohstoffe, insbesondere größere Partikel wie Äste und Stängel, müssen zunächst mit einem Holzbrecher auf die entsprechende Größe zerkleinert werden.
Trocknen
Der Feuchtigkeitsgehalt der Rohstoffe muss zwischen 8% und 12% liegen.
Überschüssige Feuchtigkeit wird mithilfe eines Trockners entfernt, bevor sie der Biomasse-Brikettiermaschine zugeführt wird.
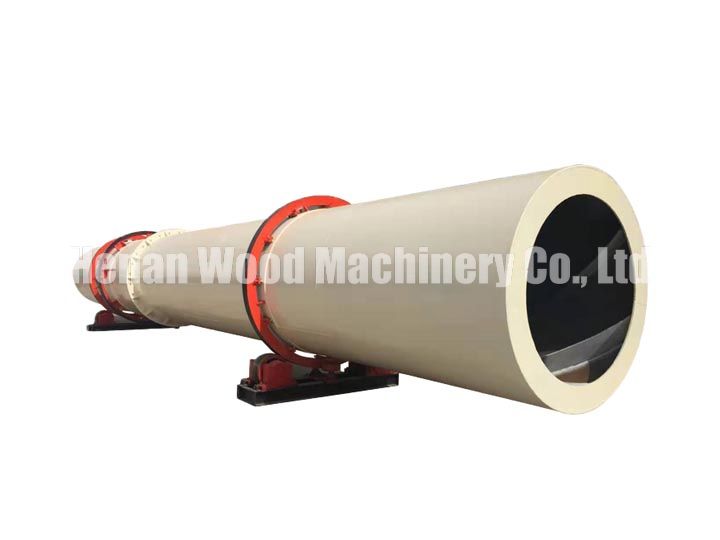
Diese Vorbereitung gewährleistet die Effizienz und Qualität der fertigen Briketts.
Struktur aus Holz Briketts Herstellungsmaschine
Der Struktur der Maschine zur Herstellung von Holzbriketts wurde entwickelt, um Leistung, Effizienz und Benutzerfreundlichkeit zu verbessern. Zu den Schlüsselkomponenten gehören.
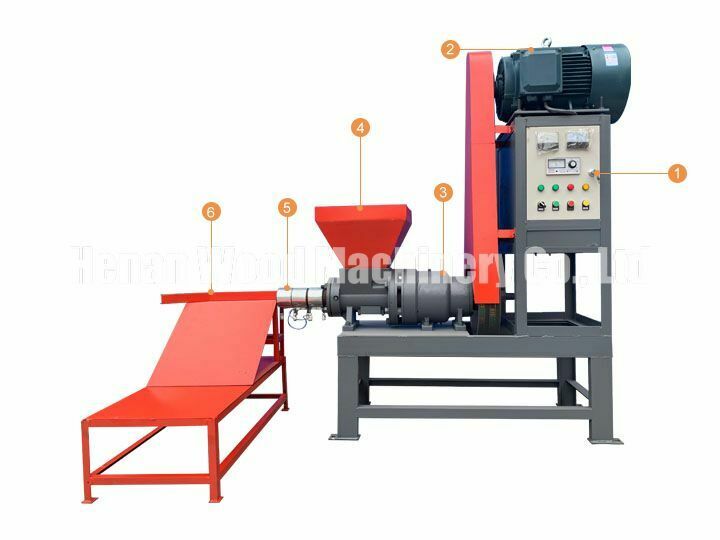
- Schaltschrank. Reguliert Spannung und Temperatur; Betreibt den Schraubenpropeller rückwärts, um ein Blockieren zu verhindern.
- Motor. Hochwertiger, schnell drehender Motor für reibungslosen Betrieb.
- Lager. Verbesserte, dickere Lager verbessern die Verschleißfestigkeit und sorgen für eine stabile Leistung.
- Futteranschluss. Das größere Design erhöht die Effizienz, indem es mehr Materialeintrag ermöglicht.
- Elektrische Heizkreise. Passt den Feuchtigkeitsgehalt automatisch an, um eine optimale Brikettqualität zu gewährleisten.
- Schneidebrett. Sammelt fertige Sägemehlbriketts nach der Verarbeitung.
Diese Komponenten arbeiten zusammen, um sicherzustellen, dass die Maschine effizient arbeitet und gleichzeitig hochwertige Briketts produziert.
Komponenten der Maschine zur Herstellung von Sägemehlbriketts
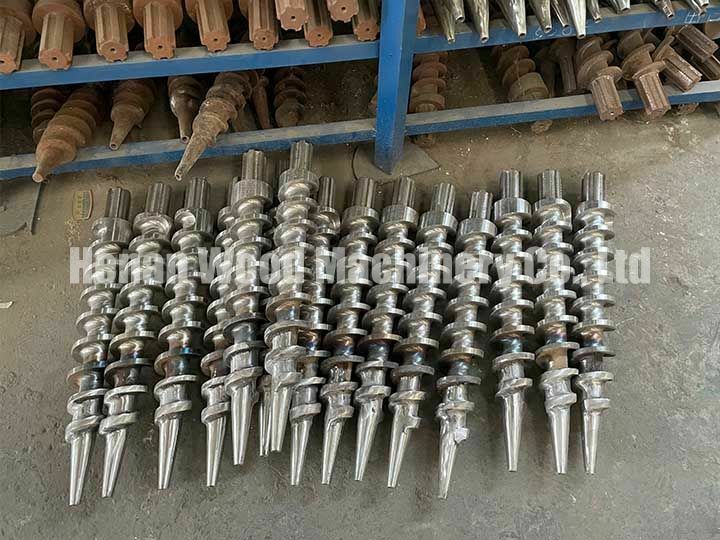
- Die Schnecke der Biomasse-Brikettiermaschine wurde mehreren Debugging-Prozessen unterzogen.
- Die Tonhöhe wurde erhöht, um die Leistung zu verbessern.
- Die Futterkapazität wurde verbessert.
- Durch diese Anpassungen konnte die Leistung der Maschine deutlich gesteigert werden.
- Das vollautomatisch gesteuerte elektrische Heizgerät ist für die Sägemehlbrikettiermaschine konzipiert.
- Es kann die Trockenheit und Feuchtigkeit des Materials regulieren.
- Diese Funktion gewährleistet eine stabile Entladung und Formung der Briketts.
- Es erhöht auch die Arbeitseffizienz der Maschine zur Herstellung von Sägemehlstäben.
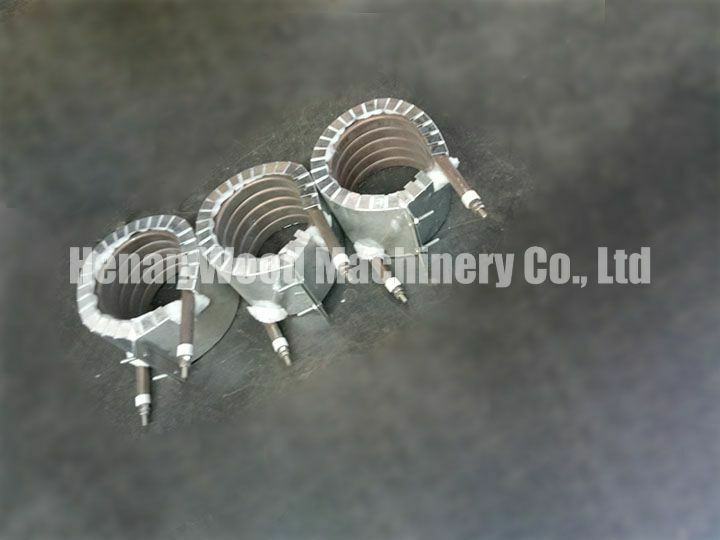
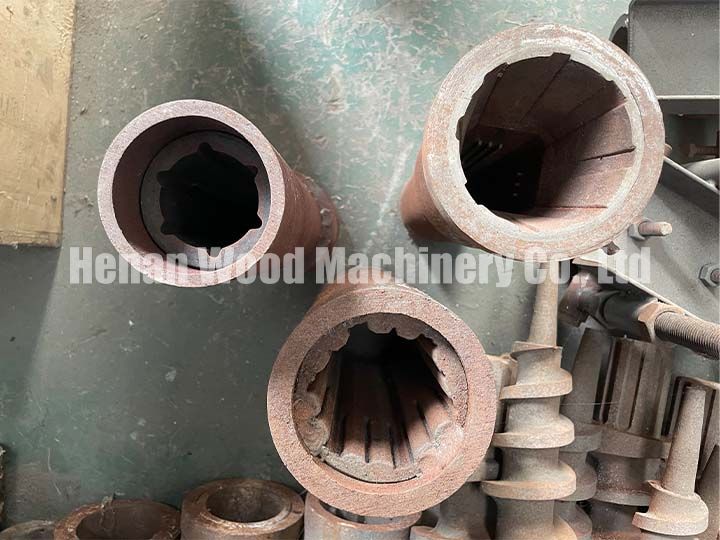
- Zu den gängigen Formen der Sägemehlbrikettiermaschine gehören sechseckige und viereckige Formen.
- Spezielle Formen können je nach Kundenwunsch angepasst werden.
- Kontinuierliches Debuggen hat zu Verbesserungen in der Struktur des Formzylinders geführt.
- Die Modifikationen reduzierten die Reibung zwischen der Maschine und dem Rohmaterial.
- Durch diese Anpassungen wurde die Dichte der erzeugten Briketts erhöht.
Prinzip der kommerziellen Biomasse-Brikettmaschine
Beim Betrieb der Sägemehlbrikettiermaschine ist eine Vorheizung auf 380 Grad Celsius erforderlich, bevor Rohstoffe in die Maschine eingespeist werden können. Sobald die gewünschte Temperatur erreicht ist, beginnt der Prozess der Brikettbildung.
Zu den wichtigsten Schritten gehören:
- Vorheizen. Die Maschine muss auf 380°C vorgeheizt werden.
- Füttern. Sobald die richtige Temperatur erreicht ist, werden die Rohstoffe in die Zufuhröffnung gegeben.
- Materielle Bewegung. Der Motor treibt das Lager und die Förderschnecke an und schiebt das Material sanft in das Formrohr.
- Extrusion. Unter hoher Temperatur und hohem Druck werden die Holzspäne oder Reishülsen durch die Auslassöffnung extrudiert und bilden die endgültigen Briketts.
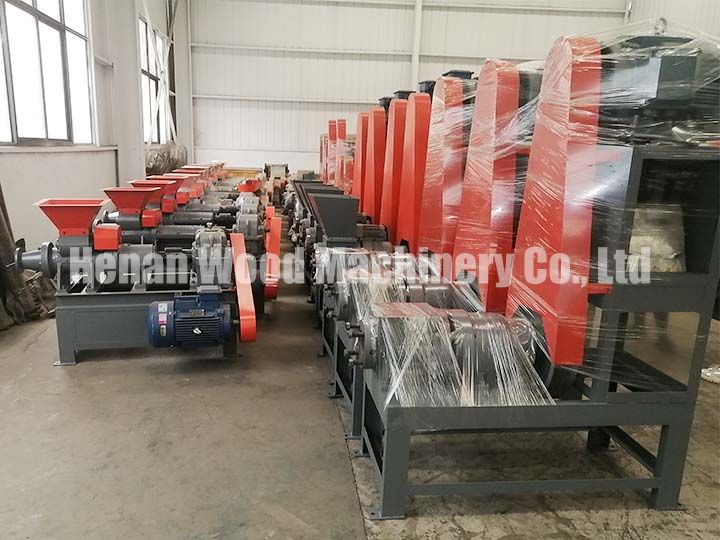
Dieser Prozess gewährleistet eine effiziente Produktion dichter und gleichmäßiger Briketts.
Merkmale der Endprodukte der Sägemehlbrikettiermaschine
- Die üblichen Größen komprimierter Sägemehlbriketts sind 40 cm oder 50 cm, mit einer Mindestlänge von 15 cm.
- Diese Briketts haben eine hohe Dichte, geringe Größe und gute Brennbarkeit und eignen sich daher ideal als Ersatz für Brennholz und Kohle, insbesondere für Kamine.
- Bei der Produktion werden Sägespäne unter hohen Temperaturen und hohem Druck komprimiert, wodurch hohle Briketts entstehen, die die Verdunstung von Wasserdampf unterstützen.
- Typische Außendurchmesser reichen von 50–60 mm mit Öffnungen von 15–20 mm und die Formen umfassen hohle viereckige, sechseckige, achteckige oder kreisförmige Formen.
- Qualitätsbriketts haben keine Risse, eine holzgelbe Farbe und können durch Anpassungen während der Produktion optimiert werden.
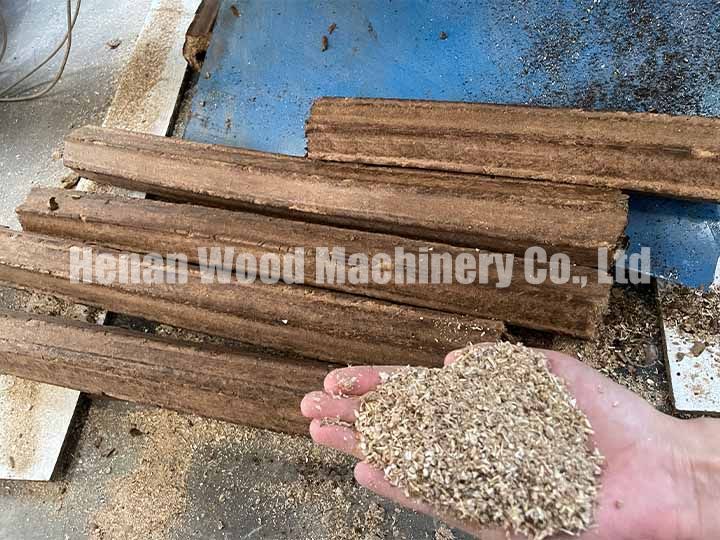
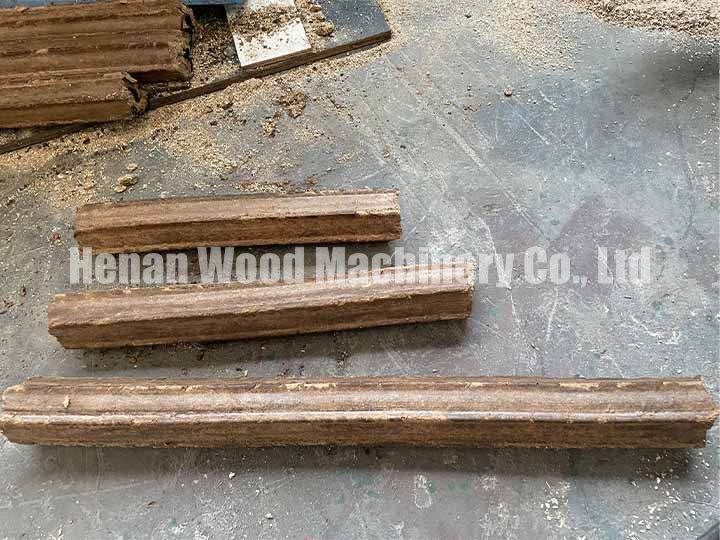
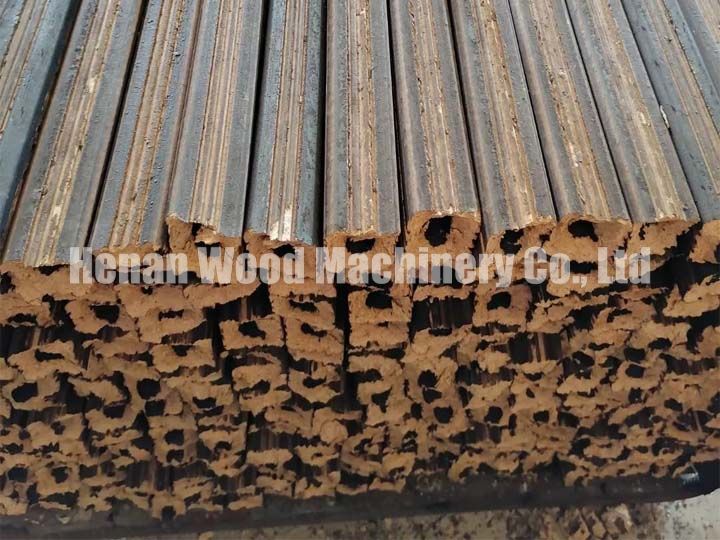
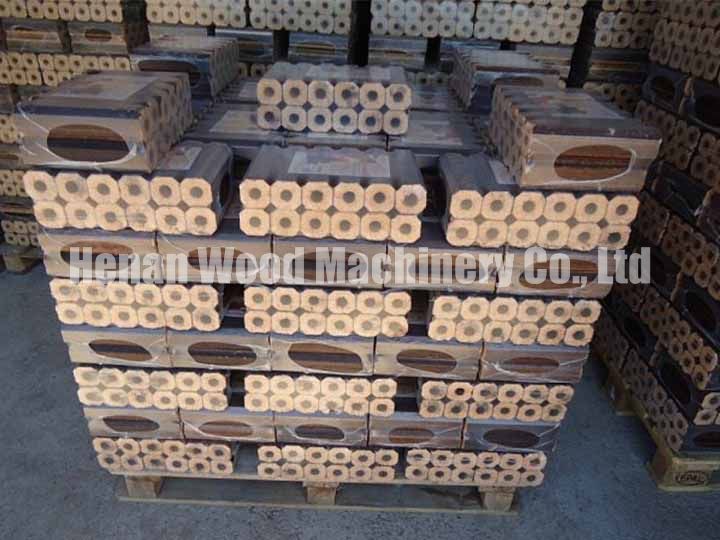
Parameter des Biomasse-Brikett-Extruders
Modell | WD-WB50 |
Kapazität | 250-350 kg pro Stunde |
Leistung | 18,5 kW/22 kW |
Abmessungen | 1,7 * 0,7 * 1,4 m |
Gewicht | 700kg |
Wie verpackt man Sägemehl-Biomasse-Briketts?
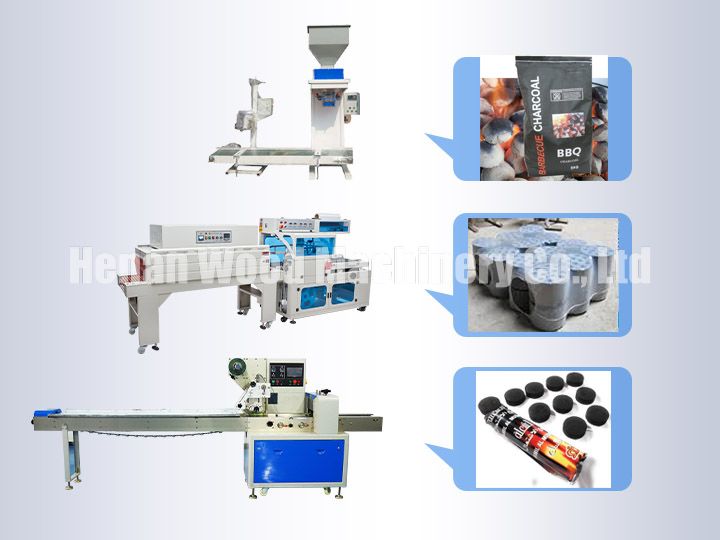
Unser Unternehmen bietet professionelle Brikettverpackungsmaschinen an, mit denen Sägemehlbriketts nach der Herstellung durch die Biomasse-Brikettmaschine effizient verpackt werden können.
Mit a Holzkohle-Verpackungsmaschinekönnen Fabriken Biobriketts in maßgeschneiderten Mengen verpacken.
Hauptvorteile der Verpackung
- Feuchtigkeitsschutz. Verpackte Briketts sind besser vor Feuchtigkeit geschützt.
- Einfacher Transport. Verpackte Briketts sind einfacher zu transportieren.
- Verbessertes Erscheinungsbild. Die Verpackung verbessert das Erscheinungsbild und macht die Briketts für den Markt attraktiver.
Diese Eigenschaften sorgen dafür, dass die verpackten Sägemehlbriketts nicht nur praktisch, sondern auch marktfreundlich sind.
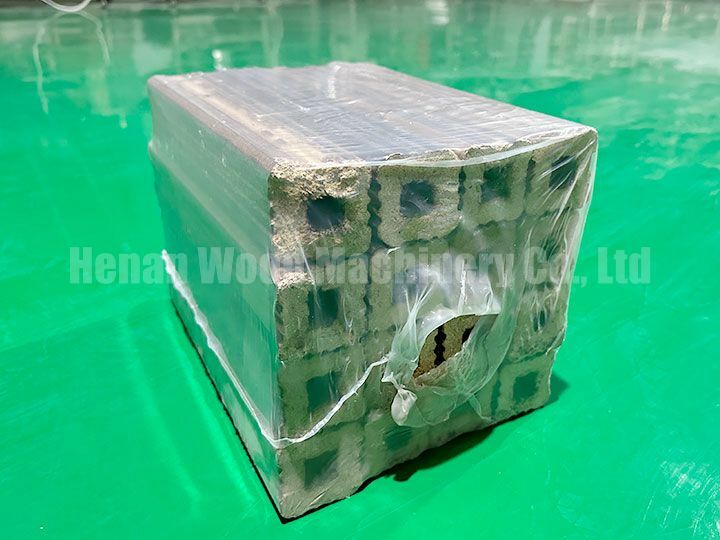
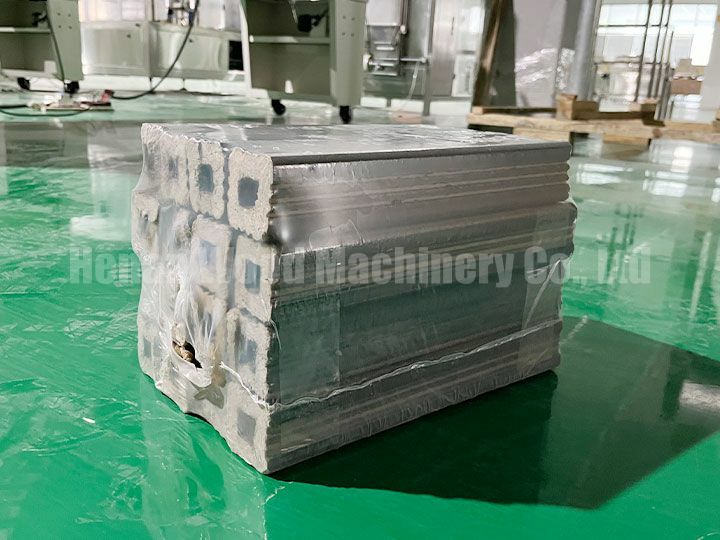

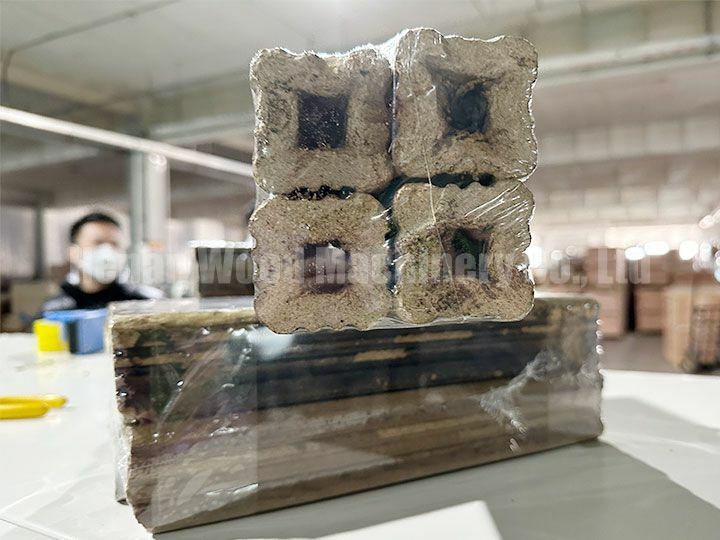
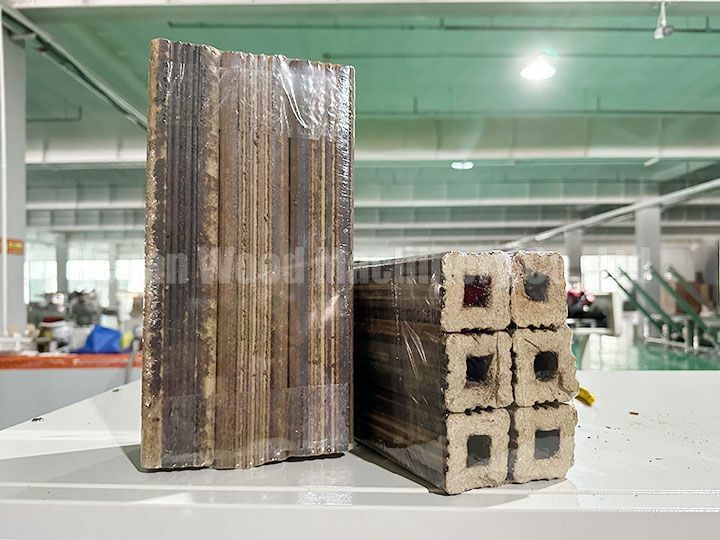

Vollständige Produktionslinie für Biomasse-Sägemehlbrikettsmaschinen
Die Sägemehlbrikettiermaschine arbeitet dadurch effizienter eine komplette Produktionslinie für Biomassebriketts. Diese Linie umfasst wichtige Geräte wie Holzzerkleinerer, Trockner und Sägemehlbrikettiermaschinen, die zum Verkauf stehen.
Die Hauptschritte im Herstellungsprozess von Sägemehl-Biomasse-Briketts sind wie folgt:
- Erste grobe Zerkleinerung. Große Baumstämme und Holzreste werden zerkleinert.
- Feine Zerkleinerung. Das zerkleinerte Material wird weiter zu kleineren Partikeln zerkleinert.
- Trocknen. Sägemehl wird getrocknet, um den optimalen Feuchtigkeitsgehalt zu erreichen.
- Kühlung. Das getrocknete Sägemehl wird gekühlt, um es zu stabilisieren.
- Brikettbildung. Das Sägemehl wird zu Briketts gepresst.
- Verkohlung. Abschließend werden die Briketts einer Karbonisierung unterzogen, um ihre Eigenschaften zu verbessern.
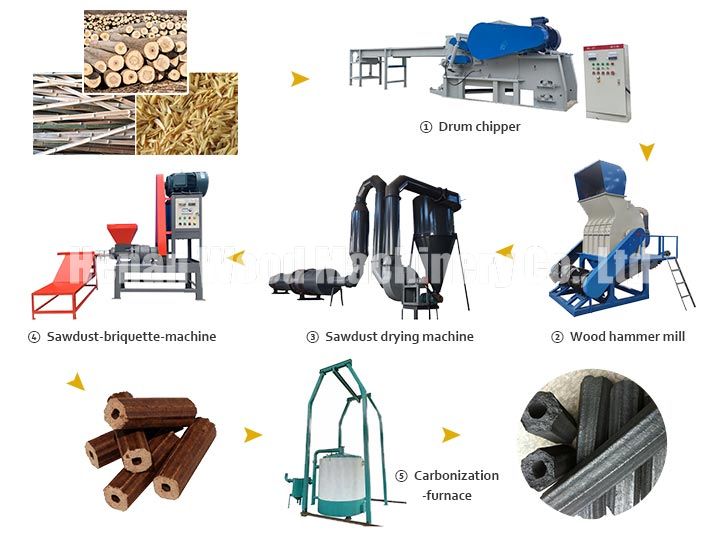
Verschiedene Materialien, darunter Baumstämme, verschiedene Hölzer und Möbelreste, werden durch diesen Prozess in Sägemehlstangen umgewandelt.
Als professioneller Hersteller und Lieferant von Biomasse-Holzkohlemaschinen kann unser Werk die Ausrüstung an spezifische Anforderungen anpassen und sowohl inländischen als auch internationalen Kunden umfassende Verarbeitungslösungen zu wettbewerbsfähigen Preisen anbieten.
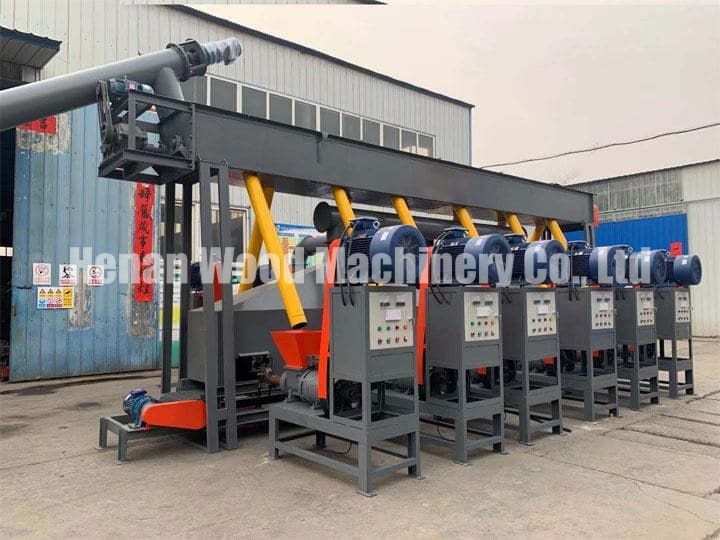
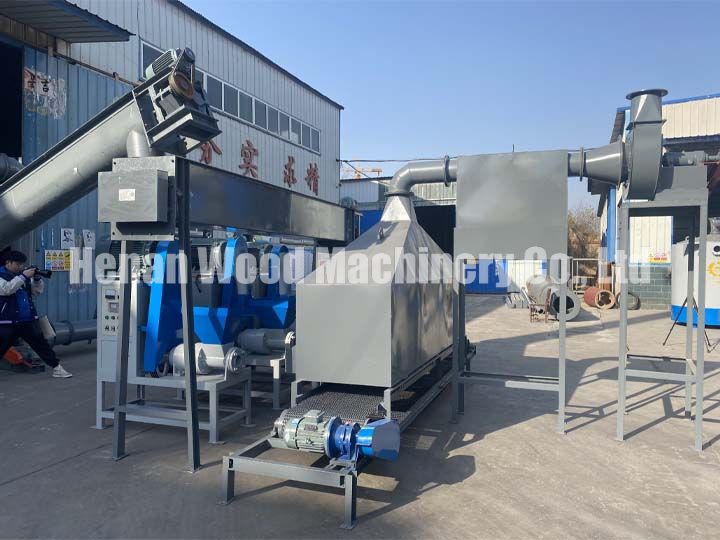
Eine komplette Holzkohleanlage zum Verkauf in Guinea installiert
Unser Unternehmen ist erfolgreich eine komplette Holzkohleproduktionslinie nach Guinea verschifft, dessen Schlüsselkomponenten fünf Sägemehl-Biomasse-Brikettiermaschinen sind. Das Holzkohlewerk in Guinea wird als Endprodukt karbonisierte Biomassebriketts produzieren.
Um einen reibungslosen Aufbau zu gewährleisten, haben wir einen unserer Ingenieure nach Guinea entsandt, um bei der Installation der gesamten Produktionslinie zu helfen. Der Kunde hat den Installationsprozess nun abgeschlossen und mit der Produktion von Holzkohlebriketts begonnen.
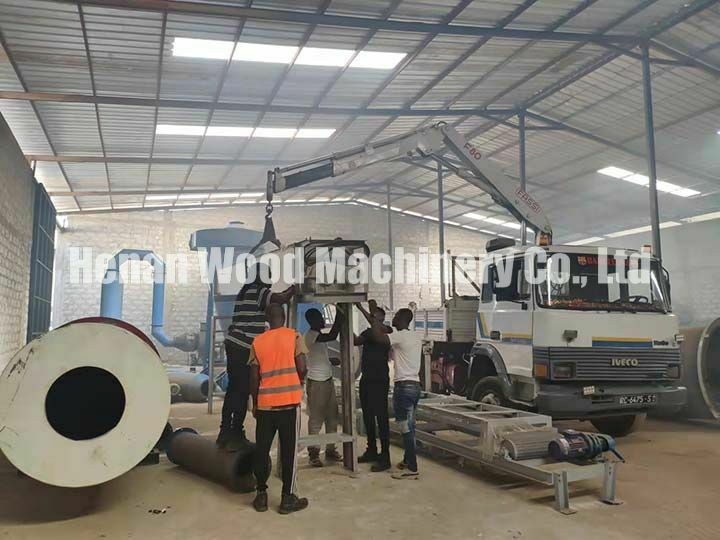
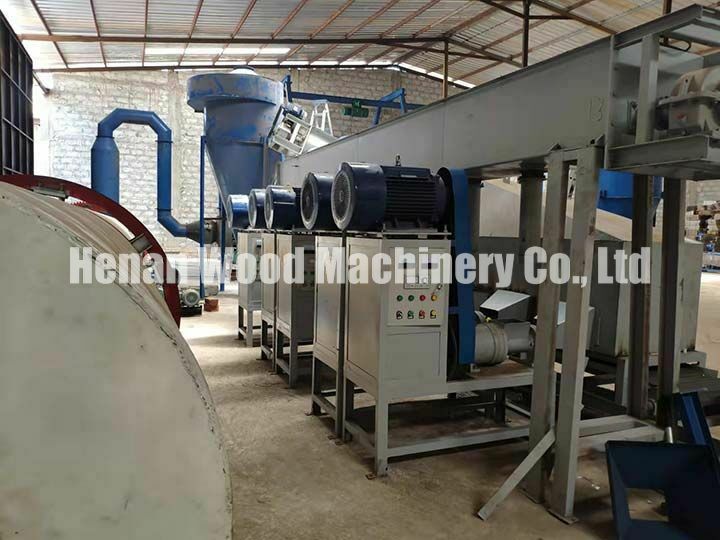
Können Rinde und Blätter zur Herstellung von Sägemehl-Biomassebriketts verwendet werden?
Nach dem Kauf einer Sägemehl-Brikettmaschine ist es für Kunden wichtig, die Eignung ihrer Rohstoffe für die Herstellung von Holzkohlebriketts zu beurteilen.
Ein indonesischer Kunde hat sich während des Kaufvorgangs an uns gewandt und Bedenken hinsichtlich der in der Nähe seiner Fabrik verfügbaren Materialien geäußert. Sie stellten fest, dass zahlreiche Bäume ihre Anlage umgaben und viele beschnittene Äste und Blätter typischerweise verbrannt wurden.
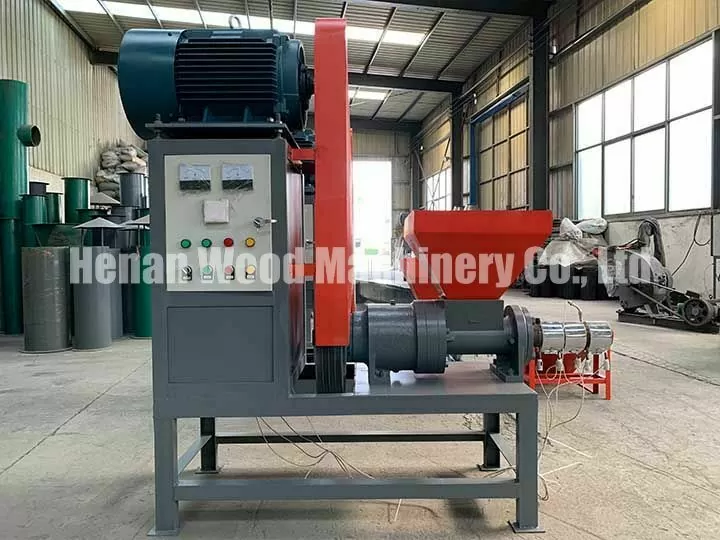
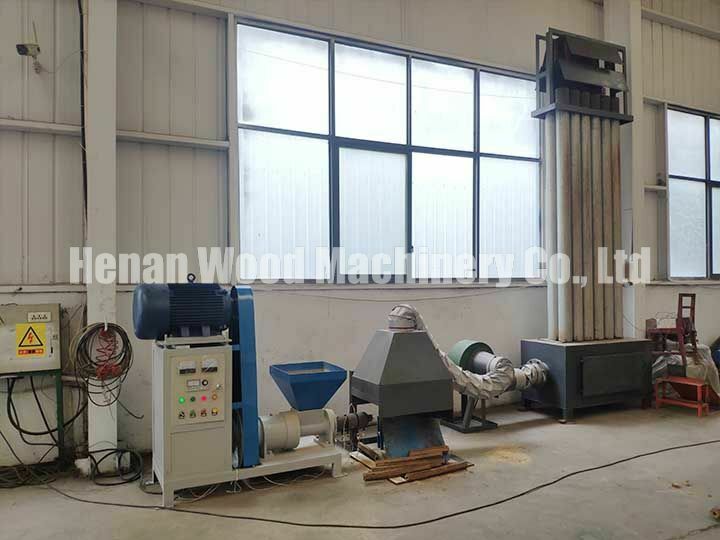
Aus Sicht des Umweltschutzes fragten sie, ob sie diese Blätter oder Rinden für die Holzkohleproduktion nutzen könnten. Die gute Nachricht ist, dass sich eine Vielzahl von Rohstoffen für die Herstellung von Holzkohle eignen, darunter:
- Sägespäne
- Maisstängel
- Blätter
- Bellt
Es ist jedoch wichtig zu beachten, dass Blätter und Rinde zwar verwendet werden können, diese jedoch mit anderen Materialien wie Sägemehl kombiniert werden sollten, um optimale Ergebnisse bei der Herstellung von Biomassebriketts zu erzielen.
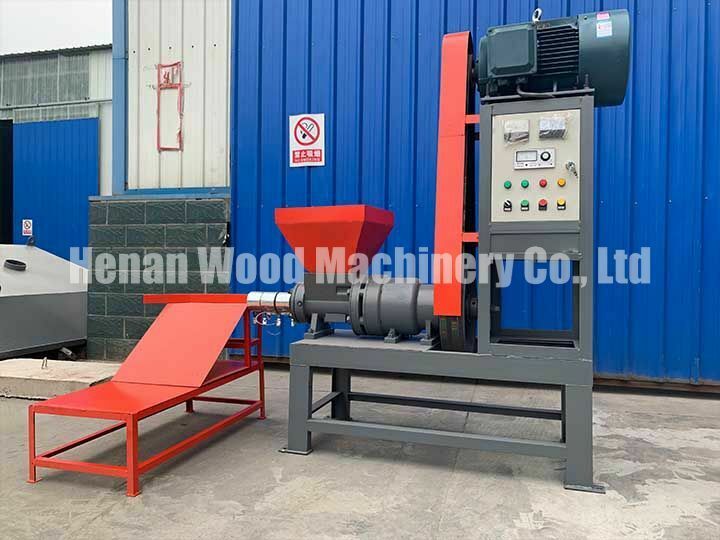
Globale Fälle von Biomasse-Brikettmaschinen für Unternehmen
Wir haben es kürzlich fertiggestellt die Lieferung einer kompletten Produktionslinie für Biomassebriketts nach Myanmar für einen Kunden, der im Holzkohlegeschäft tätig ist. Dieser Geschäftsmann betreibt vor Ort seine eigene Holzkohleverarbeitungsfabrik und hat unseren Kanal für Holzkohlemaschinen auf YouTube entdeckt, als er nach Ausrüstungslieferanten suchte.
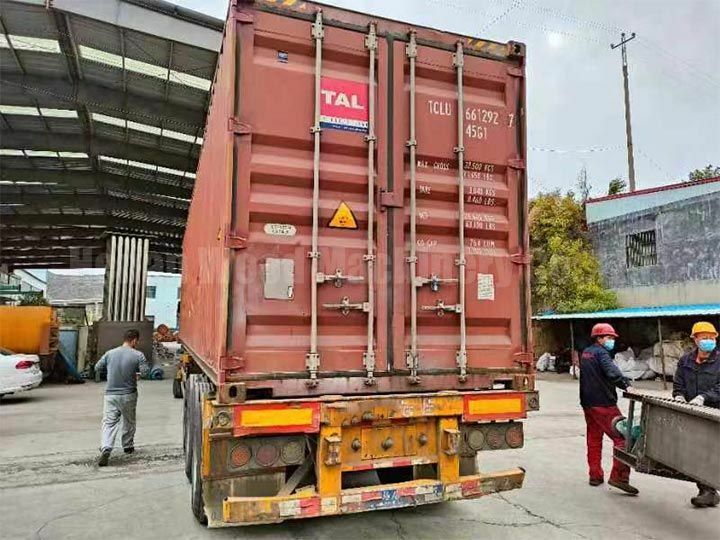
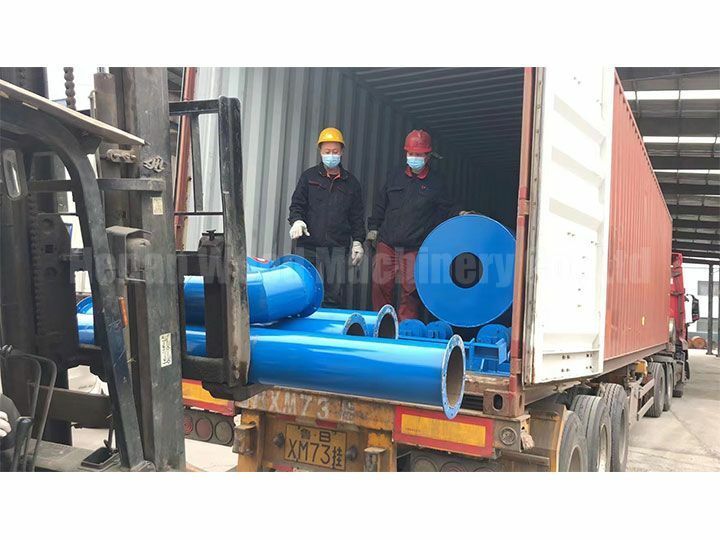
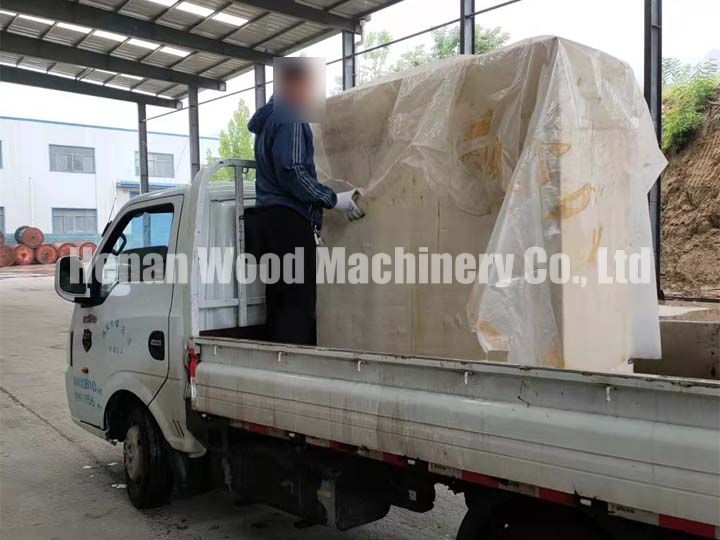
Nach ausführlichen Gesprächen mit unserem Vertriebsleiter entschied sich der Kunde für ein umfassendes Paket, das Folgendes beinhaltete:
- Sägemehlbrikettiermaschine
- Holzbrecher
- Karbonisierungsofen
- Zugehörige Zusatzausrüstung
Unsere Biomasse-Brikettmaschinen wurden in verschiedenen Ländern erfolgreich eingesetzt und unterstützen Holzkohlebetriebe und Holzverarbeitungsbetriebe bei der gewinnbringenden Herstellung von Sägemehl-Biomasse-Briketts.
Wenn Sie an ähnlichen Lösungen interessiert sind, können Sie sich jederzeit an uns wenden und sich beraten lassen.
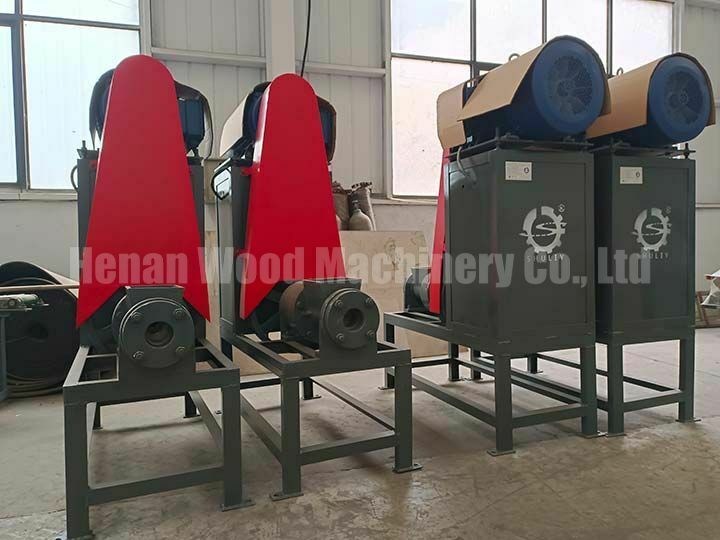
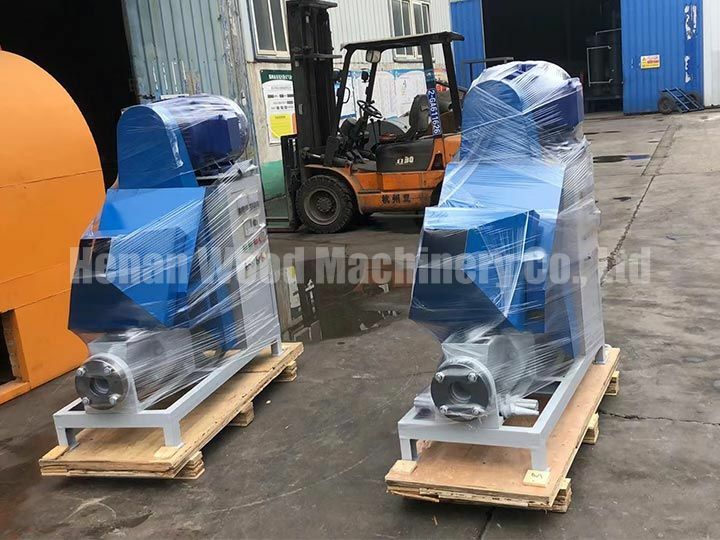
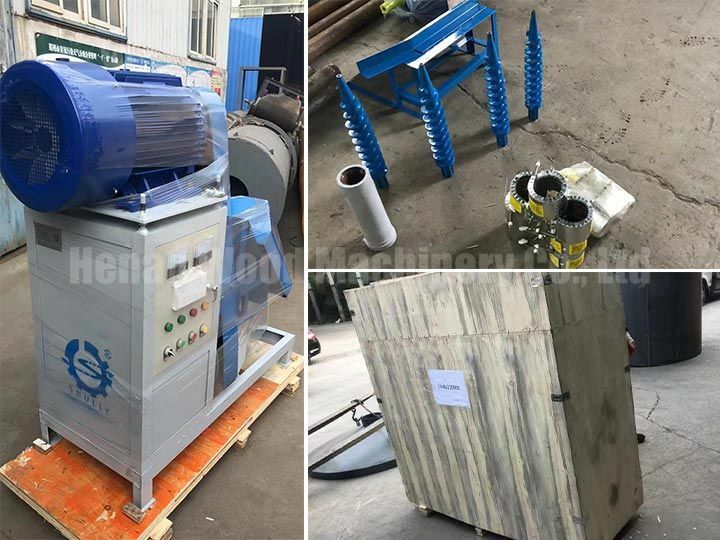
Investieren Sie in den Holzbrikett-Extruder von Shuliy
Zusammenfassend lässt sich sagen, dass unser fortschrittlicher Holzbrikett-Extruder darauf ausgelegt ist, Holzabfälle effizient in eine nachhaltige Brennstoffquelle umzuwandeln. Diese umweltfreundliche Lösung unterstützt nicht nur die Holzverarbeitung, sondern hilft Ihnen auch, Ihre Nachhaltigkeitsziele zu erreichen.
Wenn Sie Holzabfälle in eine wertvolle Ressource verwandeln möchten, ist unser Unternehmen Ihr idealer Partner. Kontaktieren Sie uns noch heute, um innovative Lösungen zu entdecken, die auf Ihre Produktionsanforderungen zugeschnitten sind.
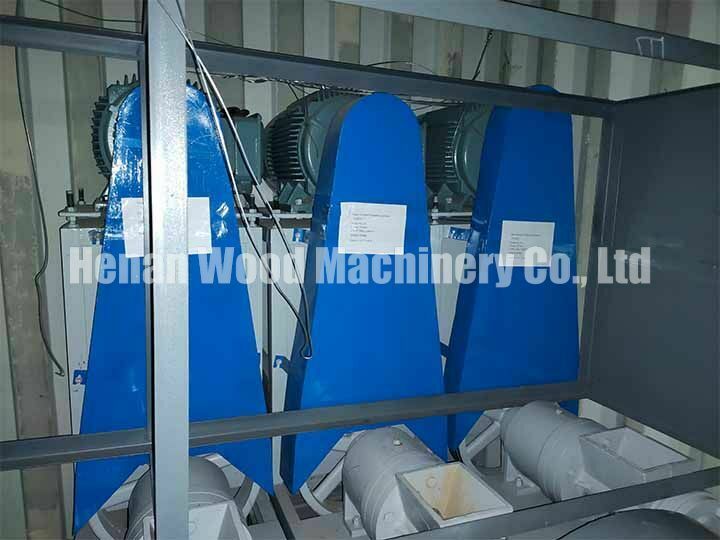
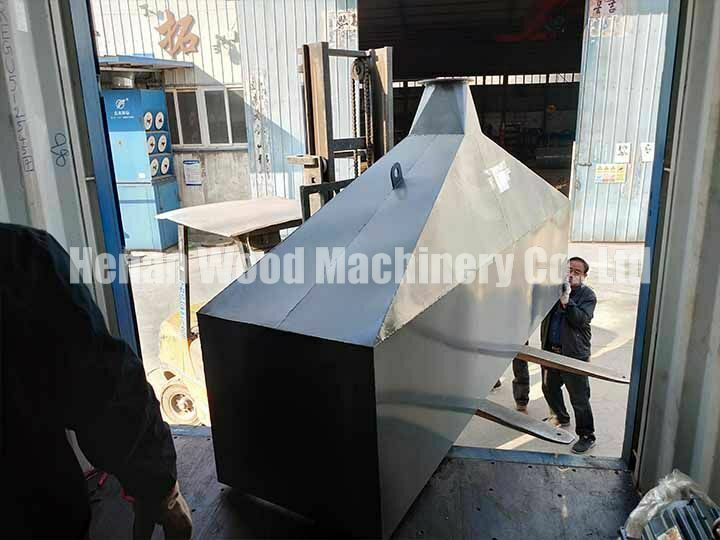